製造業・品質管理の4Mとは? 5M+1Mや6Mとの違い、変更管理、効果の出し方について解説
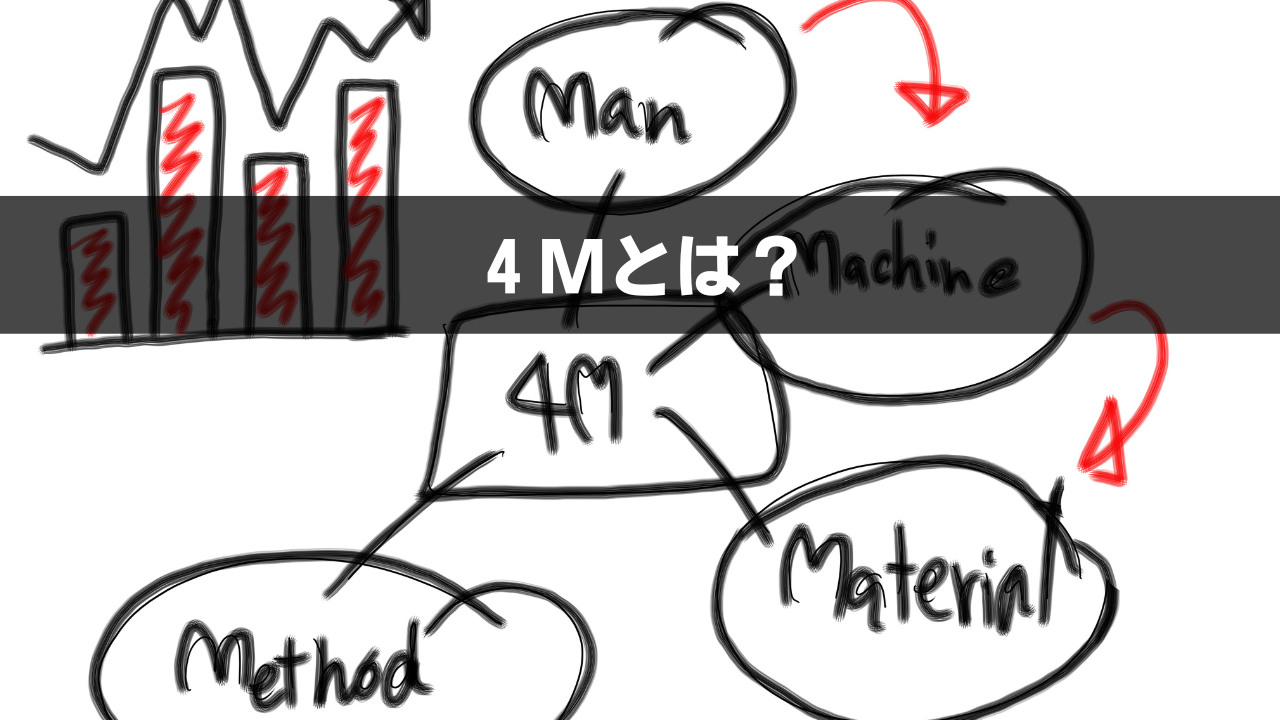
製造業において「品質」は非常に重要度が高い要素です。品質の低い製品を出荷してしまえば、低品質な製品によって顧客満足度を低下させるだけでなく、安全に関わる問題につながるリスクを負ってしまいます。
しかし、品質はさまざまな要因の影響を受けて決定されるため、その適切な管理は決して簡単なものではありません。そのことから、現在、影響要因を抜けもれなく管理する「4M」を用いて品質を管理する企業が増えています。
この記事では、4Mの概要や4Mを用いた品質管理のメリット、また、4Mを用いた変更点管理について解説します。
4Mとは?
4Mとは、「Man」「Machine」「Material」「Method」の頭文字をとったもので、製造現場や生産現場で必要不可欠な品質管理業務を行う際に有用なフレームワークです。
4Mは、主に製造業で採用されているフレームワークですが、各要素の解釈を変更することで物流業など他の業種にも応用できます。
Man(人)
「Man(人)」は、製造現場における作業者を意味します。Manには、設備を操作する人だけでなく、部品や完成品を運搬する人、工場設備の保全担当者、管理者などさまざまな業種の人が含まれます。そして、Manは、4Mの中でも唯一、4Mのフレームワークにおいて定義される他の要素を扱うことができる要素です。
Manの中で品質管理に直接的な影響を与える要素としては、個人的なものと組織的なものの大きく二つが挙げられます。個人的なものは、作業者の保有スキルや勤務状況、モチベーションなど。組織的なものは、作業者の配置などです。
Machine(機械)
「Machine(機械)」は、製造現場における製造設備や機械工具などを指します。製造設備や機械工具は、作業品質や製品品質だけではなく、生産性や作業者の安全にも影響を与えます。
Machineの中で品質管理に影響を与えるものとしては、設備や工具単体に加えて、工程内の設備レイアウトや設備と工具の組み合わせなどが挙げられます。
Material(材料)
「Material(材料)」は、製品に用いられる材料に関する要素です。原材料の品質は、製品の品質に直結するため、適切な管理が必要です。例えば、保管状態によって変化が生じる原材料の管理や原材料の在庫管理は品質に大きく影響します。
また、適切な品質管理を行うためには、製品と製品の原材料との紐づけをきちんと行うことが重要となります。紐づけは、製品と原材料との紐づけはデジタル技術を用いることで効果的に行うことが可能です。
Method(方法)
「Method(方法)」は、製造現場におけるさまざまな方法や手段をさします。具体的には、生産形態や生産方式、作業のプロセスやルール、検査方法など多岐にわたります。
Methodの観点では、作業手順が適正化されているだけでは不十分とみなします。設備の配置や作業員のスキル、原材料に見合った方法の選択など、さまざまな要素も鑑みて手法・手段の最適化が必要ということです。
また、Methodの観点で品質管理の最適化を進めるためには、特定の作業員による属人化を予防する必要があります。作業手順やプロセスを標準化したうえで、管理体制の構築も行いましょう。
安全工学における4Mとの違い
ここまで紹介した4Mに加え、安全工学においても4Mとよばれる用語があります。混同しないように注意が必要です。
安全工学における4Mは、「Man(人的要因)」「Machine(設備的要因)」「Media(作業的要因)」「Management(管理的要因)」を指します。ManとMachineは共通ですが、それ以外は異なります。
安全工学における4Mの各要素を分析・最適化することは、品質事故やヒューマンエラーの防止につながります。こちらも覚えておくといいでしょう。
4Mと5M+1Eと6Mの違い
4Mには、その発展形として「5M+1E」や「6M」といったフレームワークがあります。4Mとあわせてこれらも理解しておくことで、自社の状況に対してふさわしいフレームワークを活用することができるでしょう。
5M+1Eとは
「5M+1E」は、4Mに対して「Measurement(計測)」と「Environment(環境)」を加えたものです。
「Measurement」には、製造条件の測定や検査の測定に関する要素を包含しています。また、計測を行うこと自体の正確性も意味しています。
一方、「Environment」には、温度、湿度、振動、明度、気圧、騒音など職場環境に関する要素が含まれており、これらの要素を適切にコントロールすることで、作業員が働きやすい環境の構築が可能となります。
6Mとは
「6M」は、4Mに「Measurement」を加えた5Mにさらに「Management(管理)」を加えたものです。
製造業では、扱う製品の種類や生産体制によって、製造ラインや製造プロセスが複雑化します。特に多品種少量生産の場合には、工程や資源配分の最適化が必須となります。
このとき、個別の要素を最適化するだけではなく、全体を管理し最適化する能力が求められます。そのため、6Mでは、「Management」の項目を独立させ、重点的に意識できるようにしています。
具体的には、製造ラインの構築や人員管理などが挙げられます。中長期的な視野で企業戦略の視点に立った「Management」を行うことが重要と言えます。
4Mで品質管理を行うメリット・効果
4Mの観点で品質管理を行うことで、どのようなメリットや効果があるかを紹介します。
品質向上
品質向上を目指すためには、原材料の入荷から製品を納入するすべてのプロセスにおいて、4Mの観点で品質管理を行うことが効果的です。品質管理に抜け漏れがあると、製品に必要な品質を確保できなくなってしまいます。
4Mの観点から管理項目を分析・抽出することで、抜け漏れのない品質管理を行うことができる、品質向上につながります。
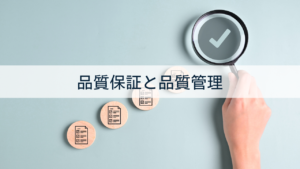
顧客満足度向上
4Mの観点で抜け漏れなく品質管理を行うことができれば、高い品質の製品を顧客に納入し続けることが可能となります。その結果、顧客からの評価が高まり、顧客満足度の向上につながります。
顧客満足度が向上すれば、当該顧客からの受注量の増加や紹介による新たな顧客の誕生などによって売上や利益の増加を実現できます。
生産性向上
4Mの観点で品質管理を進めていくと、無駄な作業の廃止や原材料管理の最適化、作業員のスキル向上や配置最適化を行うことができます。その結果、生産性向上を実現できます。
品質管理には時間をかけて丁寧に行うイメージがあり、生産性向上と品質向上がイコールで結ばれない印象を持っているかもしれません。しかし、品質管理は管理作業の効率化を促すため、高い品質と生産性向上を両立できます。
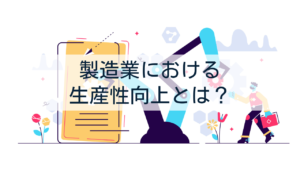
安全性向上
製造業において従業員の安全はもっとも優先されるべきものです。そのため、4Mによって管理を行う際にも安全性に十分配慮した取り組みが必要です。
例えば、設備レイアウトや作業手順の見直しを行う際には、品質や業務効率化に加えて作業員が安全に作業を行えるようにすることを十分に意識しましょう。
製造コスト削減
品質と製造コストの両立は難しいように感じるかもしれません。実際、良い原材料は原価が高いですし、品質向上のためにはその分長く検査時間を確保する必要があります
しかし、4Mの観点で分析を行えば、製造コスト削減をしつつ品質を安定化させる方法を見つけられる可能性があります。例えば、人員配置の最適化やスキル向上による作業の効率化、在庫の適正化による管理費の低減などは、品質と製造コストの両立につながるでしょう。
4Mを用いた変更管理・変化点管理とは
生産工場におけるさまざまな要素は、常に一定の状態を保てるわけではなく、何らかの要因で変化が生じるものです。これらの変更管理・変化点管理を4Mの観点で行うことで、変化・変更による影響を明確にし、効果的な対策を取ることが可能です。
Man(人)
「Man(人)」の観点では、退職や休職、配置換えなど入れ替わりが頻繁に生じます。また、業務経験によって能力が異なるため、作業品質や作業効率に大きな影響を与える可能性があります。
人の入れ替わりがあったり習熟度が異なったりしても、一定品質の作業レベルを確保する必要があります。そのためには、マニュアルの作成と使用の徹底が効果的です。また、従業員それぞれの保有スキルを管理した上で配置の変更や教育を行えば、変更・変化による影響を抑えられるでしょう。
Machine(機械)
「Machine(機械)」の観点では、新たな製造設備や機械工具の導入、経年変化、メンテナンスによる影響などで変化が生じます。
また、同じ用途の設備であったとしても仕様には現れないレベルの機差が、品質を管理する上では重要な影響を与える場合があります。
すべての設備、工具を管理するのは難しいため、管理・メンテナンスの優先順位やルールを定め、性能確認やメンテナンスを行うことが重要です。
Material(材料)
「Material(材料)」の観点では、仕入れ先の変更や原材料の品質変化などが変化点・変更点として挙げられます。また、入荷後の管理状態によっても状態が変化する可能性があるため、注意が必要です。
原材料が変化していることに気づかず従来と同じプロセス・条件で製造すると、従来とは異なる品質の製品になってしまいます。プロセス・条件を変えていないのに品質が変わった場合には、原材料の変化がないか確認し、状況に応じてプロセスの調整を行いましょう。
Method(方法)
作業手順やプロセスが標準化されていなかったり、マニュアルがあっても内容が不十分だったりする場合には、作業者の違いによって「Method(方法)」が変わってしまうことがあります。
この場合、内容の充実したマニュアルを作成して、作業者・管理者の双方に展開することで周知を徹底し、手順を標準化することが効果的です。
また、意図して作業プロセスを変更した場合には、従業員が慣れていないためミスが生じやすくなります。このような場合には、通常時よりも確認の工程を増やすなどの工夫が必要です。
4Mによって品質管理の効果を高める方法
4Mの観点による品質管理は効果的ですが、他の手法・ツールと組み合わせることでさらに大きな効果が期待できます。
AI・IoTなど最新技術の活用
近年は、製造業の工場においてもAIやIoTといったデジタル技術の導入が盛んに行われています。
これらのデジタル技術を活用することで、4Mに生じる変化を明確に検知し、速やかに分析することが可能となります。例えば、作業者の勘やコツをデータに基いて分析することで、可視化することができます。また、設備の状態を細かくセンシングすることで、品質に影響を与える変化を速やかに検出することが可能です。
製造業向けにパッケージ化されたサービスはもちろん、企業向けにカスタマイズされたサービスの提供も増えているため、デジタル技術やサービスをうまく活用することで4Mによる品質管理の効果を最大化できます。
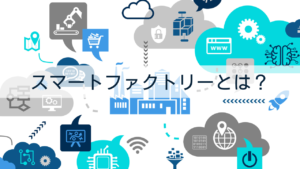
3H・5Eと組み合わせて活用
4Mの品質管理は、「3H」「5E」と組み合わせることで効果を大きくできます。
3Hとは、「初めて」「変更」「久しぶり」のことです。これらのタイミングは品質不良や事故が起きやすいタイミングとして知られています。普段よりも時間をかけたり、チェック工程を増やしたりして、十分に注意すべきでしょう。
5Eとは、「Education(教育)」「Enginnering(技術)」「Enforcement(強化・徹底)」「Example(模範・事例)」「Environment(環境)」のことで、4Mで分析した後に対策を検討する際に重視すべき観点です。
例えば、従業員への教育を新設、新たな検査技術の導入、模範事例の共有、労働環境の改善などの対策を取ることで、品質の向上につながります。
QC7つ道具・新QC7つ道具と組み合わせる
4Mと共に、「QC7つ道具」や「新QC7つ道具」をうまく併用することで、品質課題の見える化や対策検討を効果的に進められます。
例えば、特性要因図を活用することで視覚的に情報を整理し、課題の要因を明確にできます。また、パレート図を活用することで、要因の影響度を明確にし、どこから対策を行うべきか判断できるでしょう。
7つ道具のすべてのツールがどの場面でも効果的というわけではないため、状況に応じて適切なツールを選択することが重要です。
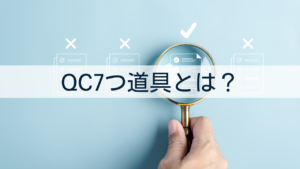
【製品の品質向上に導く「技術伝承」を、「スキル管理」で効率化しませんか?】
「技術伝承」をシステム化するなら「Skillnote」!
●スキルデータの活用で「技術伝承」の解決策がわかる
●自社に最適化したスキルマップがかんたんに作れる
●「品質向上」に成功