FMEA(故障モード影響解析)とは?実施方法やメリット、評価方法を解説

製造業において、製品や工程の品質を確保するためにFMEAは欠かすことができない重要なツールです。
この記事では、ISO9001やIATF16949におけるFMEAの概要、FMEAに期待される効果、FMEAの作成に取り組む際の注意点について解説します。
FMEA(故障モード影響解析)とは
FMEAは「Failure Mode and Effects Analysis」の頭文字を取った略称で、日本語では「故障モード影響解析」と呼ばれます。FMEAは、ISO9001やIATF16949でも扱われています。ここでは、FMEAの概要や位置づけを紹介します。
FMEAの概要
FMEAは、製品や工程の設計段階で活用する手法で、故障が生じた際にどのような問題に繋がるかを抽出・整理し、その影響を評価します。
たとえば、PCが起動しないなどの故障状態に至る基板の破壊や電源線の断線などを「故障モード」と呼びます。故障モードごとに発生した際の影響の大きさ・故障の発見のしやすさ・発生確率の観点から点数付けを行います。
この点数を基に、「設計段階においてどの故障モードを優先して避けるべきか」「どのような処置を行えば重大な事象に至らないか」といったことを検討することが可能です。
ISO9001/IATF16949におけるFMEA
FMEAは、海外の自動車メーカーや団体によって構成される国際自動車産業特別委員会であるIATFの規格IATF16949において、製品や工程の品質を確保するために重視すべき5つのコアツールの1つとして定義されています。これらのツールは互いに関連しています。FMEAを適切に扱うためには、いずれのツールも理解を深めておく必要があります。
また、IATF16949は、品質マネジメントシステムにおける国際規格である「ISO9001」をベースにして自動車関連の要求事項を追加する形で構成されているものです。FMEAでは、ISO9001においても重要な役割を担います。
具体的には、ISO9001の「8.3.3項」の「設計・開発へのインプット」において、製品やサービスの性質に起因する失敗の起こりうる結果を明確にするために、活用されています。
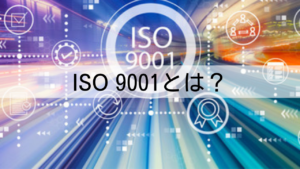
FMEAの種類
FMEAは、その適用対象に応じて以下の3種類に分類できます。それぞれの目的や特徴について解説します。
- 工程(プロセス)FMEA
- 設計(デザイン)FMEA
- 機能FMEA
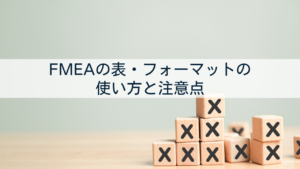
工程(プロセス)FMEA
工程(プロセス)FMEAは、製造工程における「プロセス」(作業者が行う作業や管理など)となる要素に着目して行うFMEAです。製造工程で発生する故障の原因や仕組みを追求することで、製造工程の改善を行い、品質を維持することを目的としています。
工程FMEAでは、製造工程で行われる作業を細かく分類し、それぞれの作業において生じるミスや故障に基づいて故障モードを抽出します。故障モードごとに影響を分析・評価し、必要に応じてミスや故障を防止、もしくは影響を低減するような対策を行うのが工程FMEAです。
設計(デザイン)FMEA
設計(デザイン)FMEAは、製品の設計段階で行われるFMEAです。故障モードが製品に及ぼす影響を抽出し、潜在的な事故や故障を設計段階で予測・抽出するために行われます。
各故障モードは、それによって生じる影響規模、発生確率、故障の検出確率の観点で点数付けを行い、重大な故障モードの発生を予防します。
従来は、故障モードごとに相対的な点数付けを行うことで優先順位付けを行っていました。しかし、FMEAの対象となる全故障モードの解析が完了しないと最終的な点数が確定せず、相対的な判断の基準があいまいになりやすいことから、近年は絶対評価で点数付けを行うことが増えています。
機能FMEA
設計FMEAの一部として同時に実施されることもある機能FMEAは、製品を構成するハードウェアやソフトウェアが持つ機能に基づいて、FMEAを行います。一般的な設計FMEAに比べて粒度が細かくなるため、詳細な分析が可能です。
FMEAに期待される効果
FMEAには、以下のような効果が期待されています。FMEAを作成するためにはかなりの時間が必要ですが、それ以上に大きなメリットが期待できます。
- 重大故障の未然防止
- 設計処置の優先順位付け
- 設計ノウハウの蓄積
重大故障の未然防止
FMEAで得られる最も大きな効果に、製品が潜在的に引き起こす可能性のある重大な故障の未然防止が挙げられます。FMEAで故障モードごとに付けたスコアが一定以上の場合に重大故障に分類されます。この場合には、スコアが目標値以下になるように対策を行います。
スコアを下げるには、その構成要素である「影響の大きさ」「発生確率」「見つけにくさ」に注目します。たとえば影響の大きさであれば、以下のような取組が挙げられます。
- 1つの故障では重大な影響に繋がらないようにすること
- 発生確率を下げるために寸法精度の管理や検査を厳しくすること
- 故障を速やかに発見できるように検出装置を導入すること
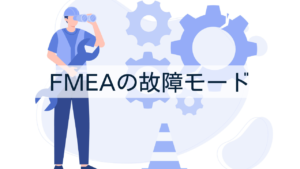
設計処置の優先順位付け
製品の開発や製造工程の構築は、限られた人員と期間で行います。そこで、重大ではない故障モードについては最低限の処置を施します。優先順位をつけて行うことが大切です。
設計処置をするための優先順位付けには、FMEAを作成する際に各故障モードに付与したスコアを活用します。
たとえば、発生確率が低くても発生した場合に、影響が大きい項目を対策すること。影響の大きさにのみ着目して、一定以上のスコアのものに関して優先的に対策を行うことは、効果的な優先順位付けであると言えます。
他には、総合スコアの大きさに応じて、優先順位を付けることなどが考えられます。
設計ノウハウの蓄積
FMEAに期待される効果に、設計ノウハウの蓄積があります。FMEAシートには、製品や工程の故障モード、その影響、検出手段、スコアといった設計開発に関する重要情報が多数記載されています。
FMEAの作成をとおして製品設計に関するノウハウを蓄積し、それをFMEAシート上に残すことができます。
ここで蓄積された情報は、従業員の教育に加えて類似製品や次世代製品を開発する際にも役に立ちます。対策が難しい故障モードを避けて基礎設計を行い、製品の品質を高めるために活用できます。
FMEAとFTAの違い
FTA(Fault Tree Analysis)は、製品やシステムの故障やトラブルを事前に想定して、故障モードから故障の根本原因をトップダウン方式で特定する手法のことです。要員の因果関係をツリー状に作成した「FT図(英:Fault Tree Diagram)」を用いることから、「故障の木解析」とも呼ばれます。FTAは設計段階に加えて、製品の使用時に発生したトラブルの分析にも用いられます。
一方、FMEAは、製品を構成する要素である部品に生じうる「故障モード」から故障を洗い出すボトムアップ方式の解析手法です。主に設計段階での影響度分析やトラブル回避のために用いられます。
FMEAとDRBFMの違い
DRBFM(Design Review Based on Failure Mode)は、その名の通り「故障モード(Failure Mode)」をベースに「FR(Design Review)」を行います。トヨタグループが2001年から試行しています。DRBFMにおける「DR」は「設計審査」と訳するのが適当ですが、実際には「設計の考察・議論」として捉えるほう実態に即しています。
DRでは、変更点と変化点に着目して心配点を導き出し、起こり得る問題への対策を講じます。開発段階で問題点を発見して対策を講じることにより、トラブルを未然に防ぐことが可能です。
変更点は意図して設計や仕様を変えた点で、変化点は使用する環境が変わった点を指します。DRBFMでは以前から変化した点に着目して問題点を導き出すため、まずはどこが変わったかを明確にしなければなりません。
DEBFMでは、設計変更点に着目して問題点を明らかにして対策を講じます。そのため、従来のFMEAに比べて効率よく問題を発見して未然防止活動を行えます。一方で、設計段階から高い信頼性が確保されていることが前提条件となるため、継続的な技術蓄積が求められます。
FMEAの評価方法
FMEAの評価には、「影響度」「発生頻度」「検出の難易度」をスコアリングして掛け合わせたRPN(Risk Priority Number)を用います。
FMEAの各項目のうち、あらかじめ設定した点数以上のRPAになった項目に対しては、点数を低減するための対策を行います。
また、近年では、とくに制御製品を対象としたFMEA評価において、機能安全に関する国際規格であるISO26262の観点を考慮に入れることが多いです。FMEAにおいて汎用的で統一された評価方法は存在しません。そのため、自社の製品や目的に合った評価方法を設定することが重要です。
RPNの算出・計算式
「影響度」「発生頻度」「検出難易度」を掛け合わせて算出する「RPN」の計算式は以下です。
RPN = 影響度の評価点 × 発生頻度の評価点 × 検出難易度の評価点
算出されたRPNの数値が大きいほど、該当の故障モードの影響が大きく厳しいことを示しています。一定の点数を超える場合には、点数を下げる対策が求められます。
影響度
影響度は、分析対象となる故障モードが生じた場合にどのような影響が生じるかを評価する指標です。数値が小さいほど影響度が小さく、数値が大きいほど影響が大きい状態を表します。
発生頻度や最終的なRPNの数値が小さくても影響度が著しく大きい故障モードでは、点数を下げるための対策が必要になる場合があります。例えば、一番影響度が大きい10点がつけられるような故障モードを避けるように、設計での対策を行うということも必要です。
発生頻度
発生頻度は、分析対象となる故障モードが発生する確率を示す指標です。数値が小さいほど発生頻度が低く、数値が大きいほど発生頻度が高い状態を表します。
影響度の数値が大きい場合でも、発生頻度が著しく低い故障モードであれば最終的にRPNの数値も小さくなり、対策が不要となります。
一方で、影響度は低くても発生頻度が高く、クレームにつながるような場合には対策が必要になります。発生頻度単体ではなく、影響度やRPNと合わせて考えます。
検出難易度
検出難易度は、分析対象である故障モードの発生を発見するための難易度を示す指標です。数値が小さいほど容易に検出でき、数値が大きいほど検出が難しいことを表します。
FMEAの実施方法(進め方)
FMEAの進め方は、以下です。
FMEAの評価フォーマットを作成
まず、社内で共通で使えるような評価フォーマットを作成します。すでに統一されたフォーマットがある場合には、目的を満たせるかどうかを確認して、必要に応じて改善します。
フォーマットには、FMEAを行う目的を達成するために必要な項目をもれなく記載します。故障モードや故障の原因、評価の観点、RPNは欠かせません。設計FMEAの場合には「設計項目」、工程FMEAの場合には「対象の工程や作業内容」なども記載します。
あらかじめフォーマットを決めておくことで、FMEAの作成プロセスを社内で統一し、作成者によるばらつきを排除できます。また、共通フォーマットであれば、製品ごとの比較が容易になり、担当外の製品のFMEAも理解しやすくなります。
工程・作業内容・対象部品を記入
FMEAのフォーマットが決まったら、対象となる工程やその工程での作業内容(工程FMEA)、対象となる部品(設計FMEA)を記載します。
ここで記載する項目が、FMEAにおけるトップ項目となります。そのため、製造工程や製品を構成する全ての要素をもれなく抽出します。
工程は、製品やサービスを作る際のプロセスや手順を示し、作業内容は各工程における具体的な作業内容や手順を示します。トップ項目はFMEAに記載する情報のうち、該当する作業・部品が特定できるような粒度で記載します。そうすることで、FMEAの起点となる評価対象を明確にできます。
故障モードを記入
FMEAにおけるトップ項目が記載できたら、各項目に対する故障モードを記載します。似たような工程・部品は故障モードも共通していることが多いため、参考にします。
故障モードを記載する際には、故障や不良と混同しないように注意します。故障は故障モードが引き起こす現象であり、不良は故障モードとは無関係です。これらを混同してしまうと、リスク評価が正しくできなくなります。
故障モードに抽出もれがあると、処置が必要な場合に適切な処置が行えずに、大きな影響が生じる可能性があります。抜けもれがないように、知見者の協力を得ながら網羅的に抽出します。
影響度・発生頻度・検出難易度を記入
網羅的に抽出した各故障モードに対して、影響度や発生頻度、検出難易度の評価点を記載します。それぞれの評価点を記載する際にばらつきが出ないように、あらかじめ観点ごとに採点基準を定めておきます。
採点基準の考え方は、処置を行うかどうかの判断に直結します。そのため、責任者も巻き込んで決めていきます。
RPNを算出
各観点における評価点を記載したら、計算式に基づいてRPNを算出します。フォーマットを作成する段階で計算式を埋め込んでおくと効率的です。
RPNは、対象の故障モードに対して対策を行う必要があるかどうかを判断する数値です。点数に応じて実行する対策は事前に決めておきます。
使用する状況や環境変化に応じて評価点が変動するような製品、サービス、工程の場合にはRPNの点数を定期的に見直します。
対策方法を検討
RPNや影響度の点数などを基に設定しておいた点数を超えた故障モードについては、点数を下げるために必要な対策を検討します。
検討の際には、「点数をいかにして下げるか」という観点だけではなく、工数やコストも考慮します。
対策案を検討し終えたら、評価実験を行って検証します。対策後には再度RPNを算出して基準を満たすかどうか確認します。
関係者とのレビュー
FMEAが完成したら、関係者とレビューを行い、記載内容を検証します。FMEAのレビューでは、チェックする観点を明確にしておきます。
顧客からFMEAの提出が求められる場合には、機密事項を除外した上で、顧客とレビューを行います。
記載内容の修正
関係者とのレビューが完了したら、記載内容を修正しまてFEMAを完成させます。
その際、同じ意味合いの事象は同じ言葉で表現するなど、細かな点にも注意します。このように記載内容を統一しておくことで可読性が高められます。
FMEAに取り組む際の注意点
FMEAの作成・実行には時間がかかります。効率的に運用するに、人によるばらつきの排除や作業重複を避けることなどを意識して取り組むことが大切です。
たとえば、あらかじめ故障モードや検出手段ごとにグルーピングを行い、それぞれのグループごとに入力項目を自動化しておけば、記載もれや人によるばらつきを排除できます。
まとめ
重大な故障を取り除き、製品の品質を確保するために、FMEAは欠かせない取り組みです。
FMEAの作成は、製品に関する幅広い知識や経験が必要なため、一筋縄ではいきません。目的に合ったFMEAを選択し、この記事で紹介したように工夫して取り組むことで、品質確保や性能向上にも貢献するではずです。
監査の指摘がゼロに!システム化で抜け漏れのないISO力量管理を実現
「Skillnote」でISO力量管理業務を圧倒的に効率化!
●バラバラだったスキルや教育訓練記録をシステムで一元管理
●ペーパーレス化の実現によって共有もラクラク
●スキルと教育が紐づいて運用の手間がなくなる
よくある質問
- FMEAにおける故障モードとは?
-
FMEAにおける故障モード(影響解析)とは? FMEAにおいて故障モードとは、製品や工程の故障状態を引き起こす構成部品・構成要素の破壊やミスなどをさします。 故障モードを考える対象は設計FMEAと工程FMEAで異なっており、設計FMEAでは製品を構成する要素である部品を対象として故障モードを抽出します。
- 不良モード分析とは何ですか?
-
「不良」は故障ではなく、そもそも狙い通りの設計が実現できていない場合や作業者への指示が間違っている状態により、期待する機能を実現できていない状態を指します。
FMEAにおける故障モードを初めて抽出する場合には、「故障」や「不良」と混同してしまいがちです。しかし、これらは明確に区別をする必要があります。