QC7つ道具と新QC7つ道具とは?違いや手法の説明、具体例、覚え方を分かりやすく解説
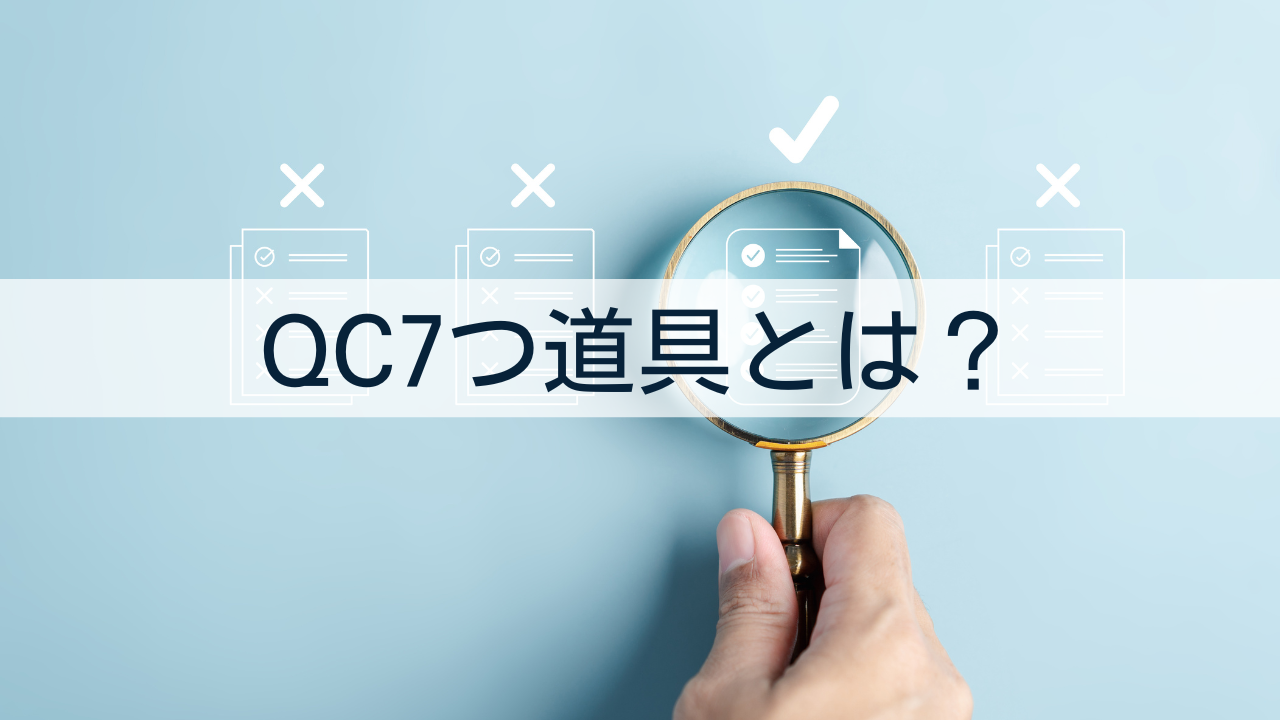
品質管理において、データによる客観的判断は欠かせません。この客観的判断を助ける7種類の代表的な手法をQC7つ道具と呼びます。QC7つ道具を用いることで、判断精度の向上や属人化からの脱却が見込めます。
本記事では、QC7つ道具と新QC7つ道具の各手法を紹介します。使用する場面やそれぞれの手法を使うことで「分かること」を列挙していますので、「自分の業務でどの手法が使えそうか?」といった視点から、ぜひ参考にしてください。
QC7つ道具とは?
QC7つ道具と新QC7つ道具とは?
品質を管理するためには、管理したい品質の実態を経験や勘に頼らず客観的に把握する必要があります。この客観的な把握や判断には数量データの解析が必要です。
数量データの解析にはさまざまな手法がありますが、比較的簡単で理解しやすい7つの手法をQC7つ道具と呼びます。
QC7つ道具が数量データを扱うのに対し、新QC7つ道具とは主に言語データを扱います。さまざまな要因が絡み合って全体像が掴みにくいときに使用する親和図や連関図法、複雑な工程管理を整理するときに使用するアローダイアグラムなどがあります。
QC7つ道具と新QC7つ道具では、数量データと言語データという違いはありますが、ともに品質改善活動で使用される代表的な手法と言えます。
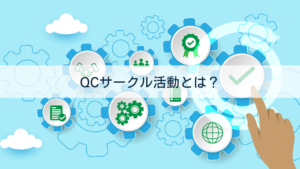
そもそもQC(品質管理)とは?
「QC(品質管理)」と聞いてまず想像されるのは製品の検査などの「製品品質の管理」ではないでしょうか。しかし、広義の品質管理、あるいは、品質保証の業務は、製品開発、供給者管理、製造の品質改善活動、出荷後のアフターフォローと多岐にわたります。
QC7つ道具や新QC7つ道具のなかには、「製品品質」という観点では使う場面が考えにくい手法も含まれています。しかし、広義の「品質保証」ととらえれば親和図などが新QC7つ道具に含まれている理由も理解できるのではないでしょうか。
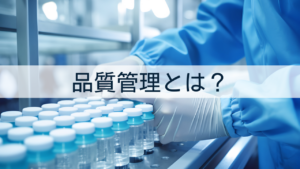
QC7つ道具の目的
QC7つ道具を使用する目的は手法によって違い、問題点の見える化、不良品・不具合の整理・分析、原因と結果の分析、改善策の効果検証など多岐にわたります。
QC7つ道具自体は1980年代に提唱された概念ですので、古いものだと感じる人も多いかもしれません。しかし、デジタル化の進んだ現代でも、データを基に判断を行うのは人間です。適切な判断を行うためにも、QC7つ道具のような基礎的な概念の十分な理解は非常に重要です。
QC7つ道具の種類
QC7つ道具を1つずつご紹介します。
ちなみにQC7つ道具を覚えるには「サンチェ監督引っ張れそう」という語呂合わせもあります。
※サン:散布図、チェ:チェックシート、監:管理図、督:特性要因図、引っ:ヒストグラム、張れ:パレート図、そう:層別・グラフ
パレート図
パレート図は縦棒と折れ線グラフを組み合わせた特殊な棒線グラフです。縦棒は要因ごとの値(発生数など)の大きさを示し、折れ線は累積割合を表します。要因は大きい順に左から並べられています。
使用目的
要因の重要度を視覚的に把握し、優先順位付けすることが目的です。イタリアの経済学者ヴィルフレド・パレートが発見した「2割の要因が8割の成功を生む」という経験則パレートの法則(80対20の法則)に基づき、どの項目が重要な2割の要因に当たるのかを見極めます。
分かること
・どの要因が最も大きな影響を与えているか
・各要因の大きさと全体に占める割合
・上位何%の要因で全体の何%をカバーできるか
使用例
・製造ラインの不良発生原因を分析し、重要な原因に対策を立てる
・苦情の種類と件数を分析し、重要な苦情に集中対応する
・プロジェクトで発生した問題の種類と件数を分析し、優先課題を発見する
このようにパレート図は、さまざまな現場で活用され、限られた資源を最も効果的な対策に注力するのに役立っています。
特性要因図
特性要因図は、フィッシュボーン図(魚の骨)とも呼ばれる分岐図です。中心に「問題の核心」を置き、原因を順次枝分かれさせて描いていきます。主要な原因から細かい要因へと階層構造化します。
使用目的
品質特性や問題に影響を与える要因を体系的に整理し、網羅的に洗い出すのが目的です。原因と結果の因果関係を視覚化して、問題の本質的な原因を探ることができます。
分かること
・問題に至る原因が階層構造で把握できる
・原因の種類と順序が分かる
・細かい要因まで漏れなく抽出できる
使用例
・製品の不具合原因を特定する
・プロセスで発生した問題の根本原因を探る
特性要因図で問題の本質的な原因に迫れますので、より的確な対策立案が可能になります。
グラフ
グラフとは、データの関係や推移を視覚的に表したものです。QC7つ道具では、棒グラフ、折れ線グラフ、円グラフなどが扱われます。
使用目的
数値データの傾向や特徴を分かりやすく表し、課題の発見や改善の程度を示すのが目的です。
分かること
・データの全体像や特徴的な動き
・異常値の有無や発生時期
・目標値との乖離状況
・前後の変化や推移
使用例
・生産数や売上げの推移を棒グラフで表す
・欠陥率や不良品発生数の変化を折れ線グラフで表す
・苦情の種類別割合を円グラフで表す
・ある期間の稼働率や達成率の推移をグラフ化する
このようにグラフは、データの特徴を視覚的にとらえやすくなるため、課題発見や改善状況の確認、要因分析などに活用されています。
ヒストグラム
ヒストグラムは、データの度数分布を棒グラフで表した図です。度数分布ではデータを範囲で区切って、範囲内でそれぞれ何件あったかを示します。ヒストグラムでは、横軸にデータを範囲ごとに区切った階級、縦軸にその階級の度数(件数)を示します。
使用目的
データの分布状況を視覚的にとらえることが目的です。正規分布からのずれや、偏りの有無、極値の存在などを確認できます。
分かること
・データの分布状態やピーク値
・データのばらつき具合
・異常値の有無
使用例
・製品の寸法や重量のばらつきを確認する
・検査データの分布状況を分析する
・サービス購入者の年齢層のばらつきを評価する
ヒストグラムから分布の特徴が一目で分かるので、データのばらつきや異常有無の確認に役立ちます。このため、工程管理や品質管理、業務改善などに活用できます。
散布図
散布図は、2つのデータ項目の関係を点で表したグラフです。横軸と縦軸にそれぞれ1つのデータ項目を取り、それらの組み合わせをプロットした図となります。
使用目的
2つのデータ項目間の関係(傾向や相関関係)を視覚的にとらえ、データが相関関係にあるかどうかを確認できます。
分かること
・2つのデータ項目間の相関の有無と強さ(正の相関、負の相関、無相関)
・外れ値(異常値)の存在
・データのばらつき具合
使用例
・製品の重量と寸法の関係を調べる
・気温と売上の相関を分析する
・医療データにおける2つの検査値の相関を確認する
このように散布図は、2つのデータ項目間の関連性を視覚的にとらえる手法です。相関分析や回帰分析の前段階で活用される場合も多くあります。
管理図
管理図とは、時系列データをプロットした折れ線グラフに、中心線(CL)と上側管理限界線(UCL)、下側管理限界線(LCL)を付けたグラフです。管理限界線とは平均値からデータの標準偏差の3倍(3σ)離れた値の線です。データの推移と、規格範囲からの外れを一目で確認できます。
使用目的
工程が統計的に安定な状態にあるのかを監視し、異常の早期発見と是正が目的です。
分かること
・データの推移とばらつき具合
・異常な変動の有無とその時期
・プロセスが統計的管理状態にあるかどうか
使用例
・製造ラインでの寸法や重量などの品質監視
管理図でプロセスの異常を迅速に察知でき、タイムリーな是正対応が可能になります。
チェックシート
チェックシートとは、集計を目的として作成された一覧表やフォームを指します。観察したい項目や発生した事象を、チェック欄にマーク(レ印や数値など)して記録していきます。
使用目的
データやタスクの実施状況を効率的に収集・集計が目的です。観察項目を体系立てて規定しておき偏りのないデータ収集が可能になります。
分かること
・事象の発生状況(件数、時間、種類など)
・タスクの実施状況
使用例
・設備の故障や異常の内容と発生時間を記録する
・品質検査での検査項目チェック
このように、チェックシートはデータ収集の手段として、さまざまな分野で活用されています。集計と分析を行う前提となる重要な手法です。
以下の表にQC7つ道具の使用場面と分かることをまとめました。適切な場面で適切な手法を使用しましょう。
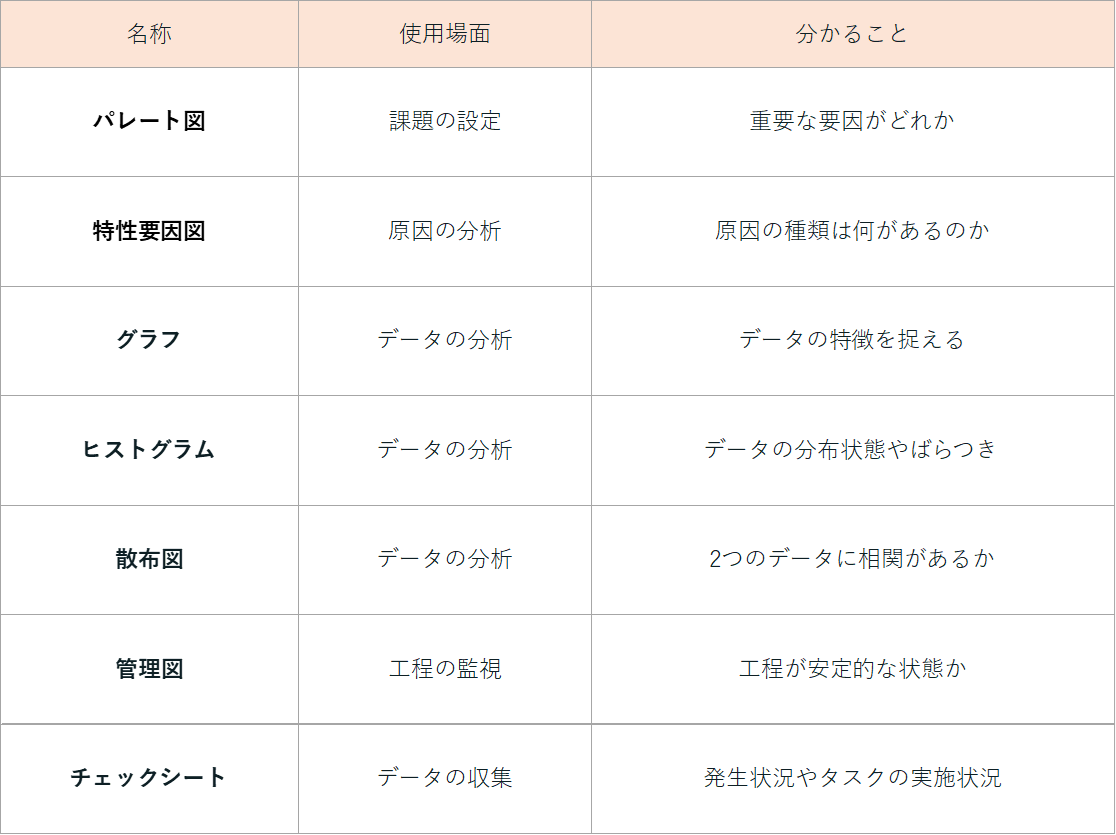
QCストーリーでのQC7つ道具の使用
製造現場では、現場での小集団活動としてQCサークル活動を行っている企業が多くあります。このQCサークル活動では、実際に現場で作業をしている作業員が中心となり、品質や効率の改善を行い、生産性を高める活動を進めます。
品質改善活動では、以下のQCストーリーに従って改善活動を行うのが、抜け漏れが少なく理想的とされています。このQCストーリーでQC7つ道具を使用する場面をご紹介します。
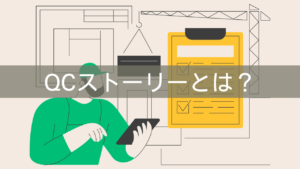
QCストーリー
テーマの選定・現状把握・目標設定
品質課題としていくつかのテーマが挙がったが、【パレート図】を用いて現状を把握し、もっとも改善インパクトの大きい不具合内容を抽出。品質改善テーマとして選定し、目標を設定した。
要因の解析
テーマとして選定した不具合内容について【特性要因図】を用いて考えうる原因を列挙した。考えうる原因に対して【グラフ】や【ヒストグラム】または【散布図】を用いてさらに要因の解析を行っていき、何に対して対策を行うべきか検討した。
対策の検討・実施
判明した不具合の発生原因に対して、対策を検討し実施した。
効果検証
【グラフ】や【ヒストグラム】、【散布図】または【管理図】を用いて、対策前後を比較し、対策の効果を検証した。
標準化
効果のあった対策について、今後も確実に実施されるよう【チェックシート】を作成し作業の標準化を行った。
反省と今後の対応
行った品質改善活動について、反省点を話し合い、次回の活動に活かしましょう。
新QC7つ道具とは
新QC7つ道具は、「新連携、アロマでP」という語呂合わせで覚えましょう。
新:親和図法、連:連関図法、携:系統図法、アロ:アローダイアグラム、マ:マトリクス図法、で:データ解析法、P:PDPC法
親和図法
親和図法とは、複数人で課題に関する発言データなどを出し合い、親和性の高いもの同士でグループ化する手法です。未経験の問題や漠然とした課題のグルーピングで全体像を把握して取り組むべき課題を導き出します。
使用目的
・問題の本質や構造、解決するべき点の整理、問題点の明確化
・参加者の共通認識の醸成
分かること
・課題の全体像
使用例
・さまざまな外部環境による経営課題の明確化
・品質不具合の要因の洗い出し
このように、親和図法は複雑な問題に対して解決の道筋を探す手法です。とくに、複数人で行った場合は皆の意見が取り入れられるため、参加者のモチベーションアップにもつながります。
連関図法
連関図法とは、複数の要因が絡み合う問題の構造を視覚的に表した手法です。中心となる問題を円で表し、その周りに関連する要因を矢印でつないだ図を描きます。要因同士の影響関係も矢印で示します。
QC7つ道具の連関図法と似た手法ですが、要因同士の関係性もつなげていきますのでより深く因果関係を明らかにできます。
使用目的
問題とその要因、要因同士の関係性を整理し、問題の構造を多角的にとらえることが目的です。要因間の影響度の大小や、重要な要因を特定できます。
分かること
・問題に関連する要因、要因同士の因果関係
・対策を打つべき重要な要因
使用例
・製品の不具合原因を多角的に分析する
・サービス改善に向けた課題の構造化する
連関図法を活用することで、複雑に絡み合う要因の全体像が視覚的にとらえられます。
系統図法
系統図法とは、達成したい目的に対して必要な手段を順序立ててツリー状に図示する手法です。必要な手段を階層的に分類・整理していき、目的を達成するための抜け漏れがないか確認します。
使用目的
達成したい目的に対し、その目的を達成するために必要な手段が明確になります。
分かること
・目的を達成するのに必要な手段
・取りうる手段の明細
使用例
・業務プロセスの作業工程を体系化する
・解決したい課題の解決策を検討する
このように系統図法は解決策の道筋や構成要素の整理などに活用されています。
マトリックス図法
マトリックス図法とは、2つの情報を行列(マトリックス)の形で組み合わせて可視化する手法です。縦軸と横軸に異なる項目を配置し、交点のセルに関連の文字情報を記入していきます。
使用目的
2つの項目間の関係性を視覚的にとらえやすくし、相互の影響や組み合わせパターンを発見しやすくします。
分かること
・2つの項目間の関連の有無と強さ
・問題や原因の所在
使用例
・製品の不具合原因と発生場所の関係性の分析
・システム要件定義における要件と機能の関連付け
このように、マトリックス図法では、2つの項目間の関係を行列形式で視覚化できるため、影響関係が発見しやすくなり、問題解決への着想につながります。
アローダイアグラム(アローダイヤグラム)
アローダイアグラムとは計画実行のタスクを矢印で結んだ図で、スケジュールを検討・管理する手法です。クリティカルパス(最重要経路)を導き出し、どの工程が遅れると全体日程に影響が出るのかを分かりやすく示せます。
使用目的
日程計画、およびその日程の管理
分かること
・綿密な日程計画、最短日数
・作業の遅れが全体に及ぼす影響
使用例
・製造工程の必要日数算出
・工期短縮の検討
このように、アローダイアグラムは複雑な日程計画から重要な情報を導き出す手法です。
PDPC法
PDPCとは、Process Decision Program Chartの略で、プロセスの意思決定を記述したフローチャートです。プロセスの流れや分岐を矢印で表します。
使用目的
業務プロセスの流れや問題が発生した際の対処法を明確化し、標準化・最適化が目的です。プロセス中の判断ポイントを明示し、適切な意思決定が行えるようにします。
分かること
・業務プロセス全体の流れ
・判断基準や次のプロセスの分岐条件
使用例
・重要設備が故障した際のフローの検討
・コールセンターの対応プロセスを標準化
PDPCにより業務プロセスが視覚化されるため、プロセス理解が深まり、標準化と最適化が図れます。原因とその後の業務の因果関係が明確になり、生産性や品質の向上につながります。
マトリックスデータ解析法
マトリックスデータ解析法とは、2つの情報を組み合わせた行列(マトリックス)の形でデータを可視化し、相関関係を分析する手法です。縦軸と横軸にそれぞれ異なる項目を取り、交点のセルにデータを入力します。新QC7つ道具の中で唯一数値データを扱います。
使用目的
2つの項目間の関係性を数値化し、視覚的にとらえることが目的です。項目間の相関の強さや、特徴的な組み合わせを発見できます。
分かること
・2つの項目間の定量的な相関関係
・相関が強い、あるいは、弱い項目の組み合わせ
使用例
・製品の不具合原因と発生場所の関係を分析
・販売商品と地域での売れ行きの相関を確認
このように、マトリックスデータ解析法では、定量的に項目間の関係が可視化できるため、特徴的な組み合わせや傾向を発見しやすくなります。
以下の表に新QC7つ道具の使用場面と分かることをまとめました。言語データを扱う新QC7つ道具では、品質管理以外にもさまざまな場面で使用できる手法が多いですね。
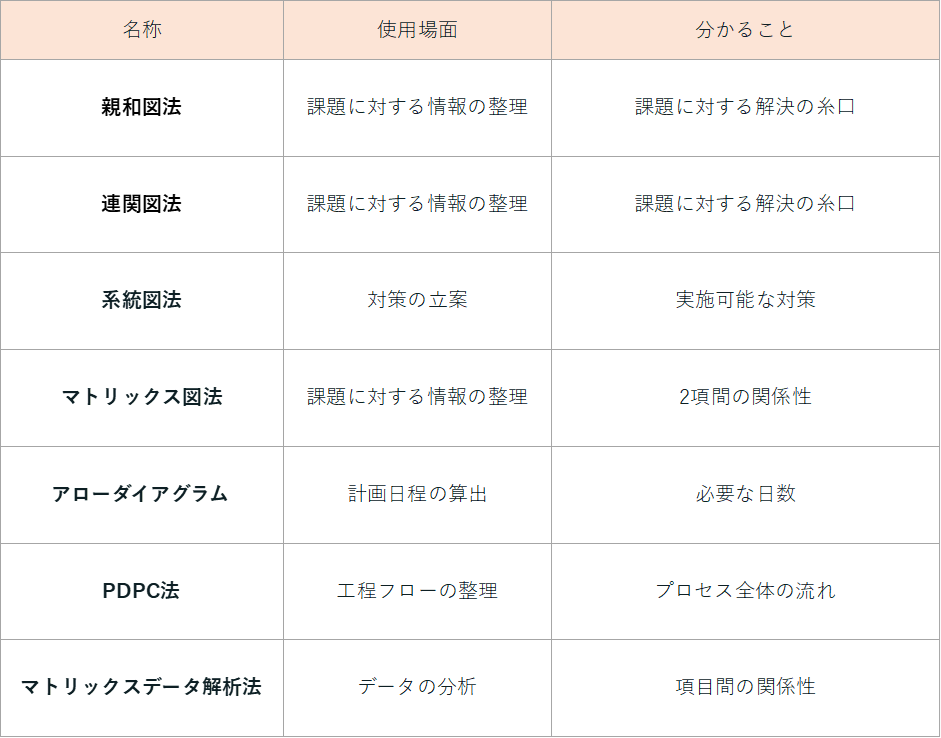
製品の品質向上に導く「技術伝承」を、「スキル管理」で効率化しませんか?
「技術伝承」をシステム化するなら「Skillnote」!
●スキルデータの活用で「技術伝承」の解決策がわかる
●自社に最適化したスキルマップがかんたんに作れる
●「品質向上」に成功した事例を大公開