MES(製造実行システム)とは? 目的と導入メリット、11の構成機能、ERPとの違い
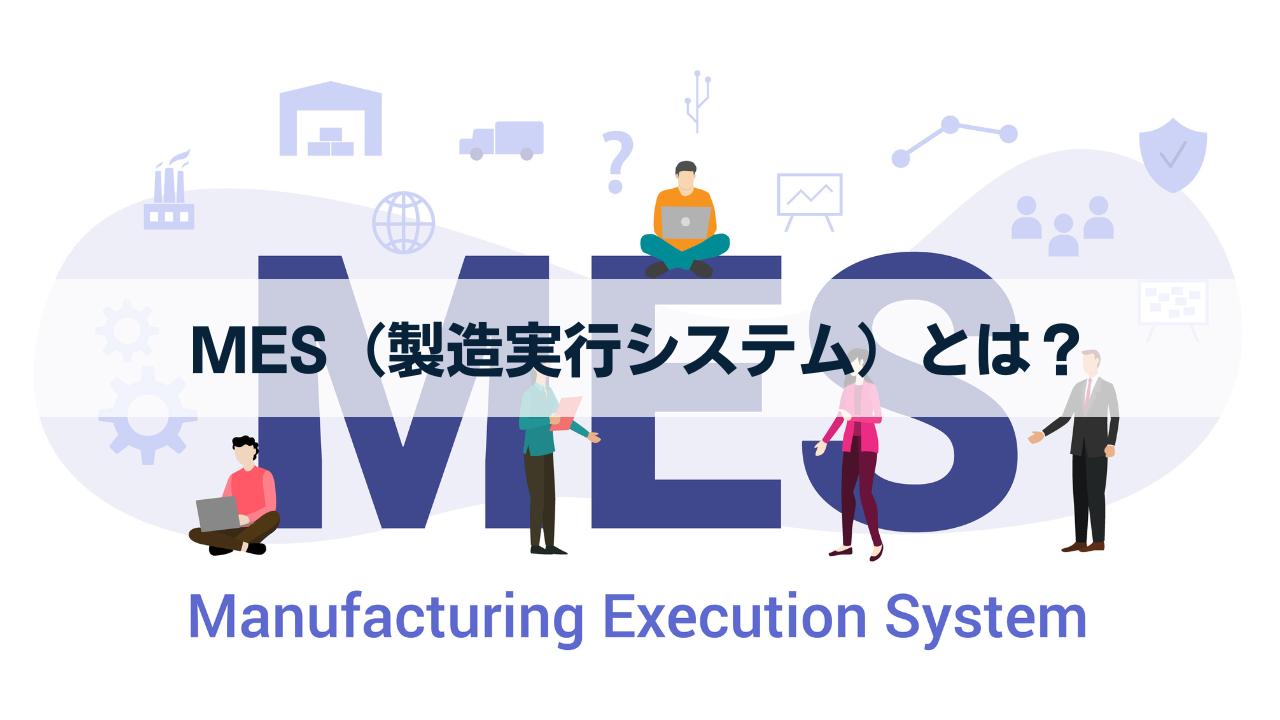
消費者ニーズの多様化により製造業のトレンドも少品種大量生産から多品種少量生産へと移行しつつあります。また、折からの人手不足によって業務の属人化を脱して多能工的な仕事の仕方が求められるようになっています。
このような状況を背景に、製造業における製造工程の業務の標準化を促す「MES(製造実行システム)」が注目を集めています。この記事では、MESの概要や必要とされる理由、導入メリット、11の構成要素、ERPとの違いなどについて解説します。
MES(製造実行システム)とは
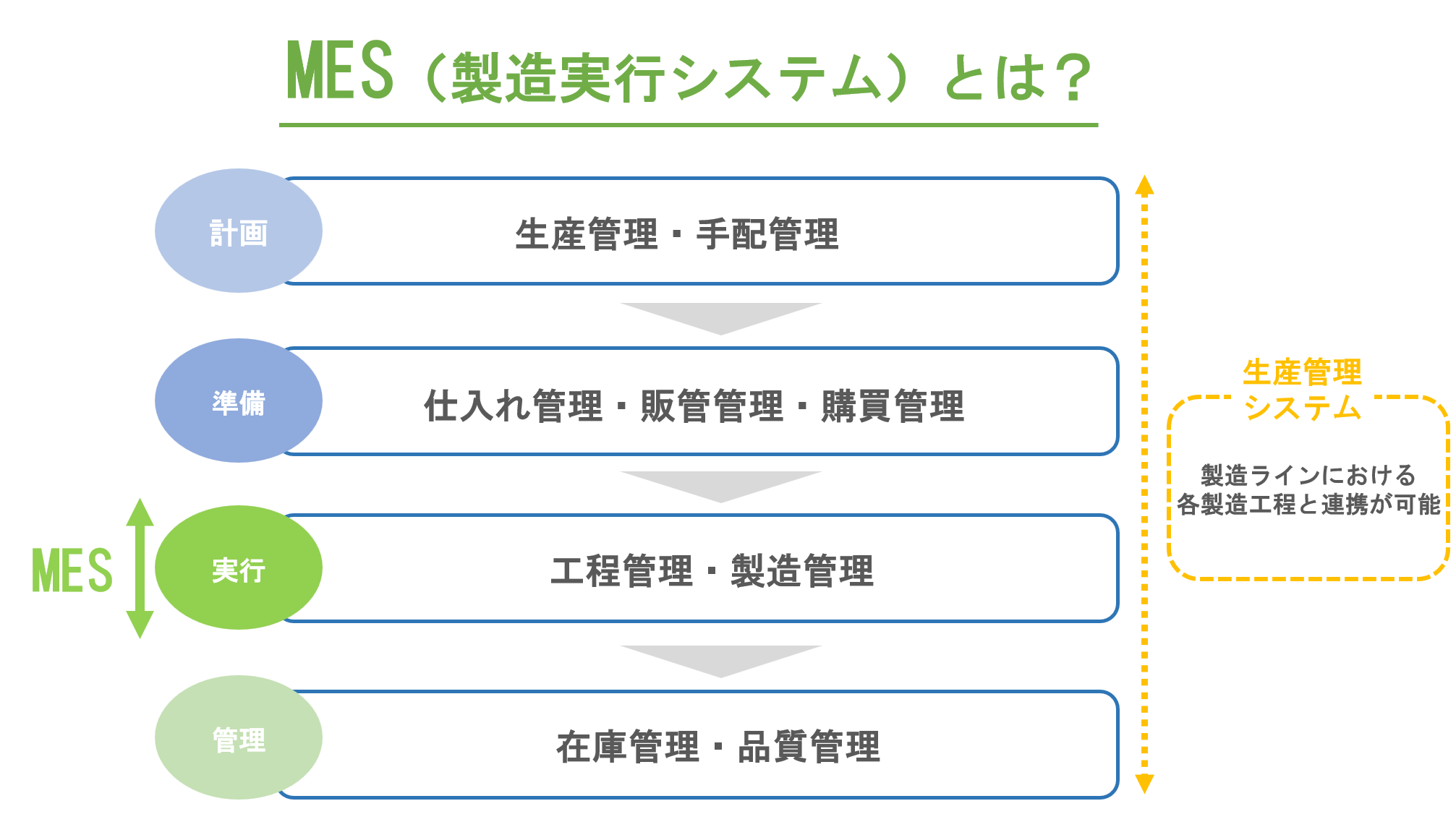
MESとは、「Manufacturing Execution System」の頭文字をとったもので、「製造実行システム」と表現されます。製造業で導入されるシステムの中でも、製造現場に特化し、業務に直結したシステムであることが特徴です。
MESの具体的な用途としては、「製造指示」「作業者の支援」「生産関連データの収集分析」「品質管理」「設備メンテナンス」などが挙げられます。
MESは、製造プロセスの可視化と業務の標準化を進め、人材も含めた限られた資源を効果的に活用できるシステムと言えます。
MESが必要とされる背景
MESが必要とされる背景には、以下のようなものがあります。
ニーズの多様化への対応
消費者のニーズが多様化したことで、従来の少品種大量生産では消費者のニーズを満たせずに競争力を維持できなくなりました。
多様なニーズに対応するためには、多品種少量生産を行う必要があります。多品種少量生産は品種が多く、少品種大量生産よりも在庫管理が難しいため、MESのような専用システムなどを用いて生産計画や在庫管理を適切に行う必要があります。
深刻な人手不足
少子高齢化に伴う労働力人口の減少による影響により、製造業に限らずさまざまな業界・企業で人手不足が深刻化しています。
限られた人材で競争力を持った製品の生産を維持するためには、業務を効率化することで生産性を向上させる必要があります。MESによる製造現場の効率化は人手不足への有効な対応策と言えます。
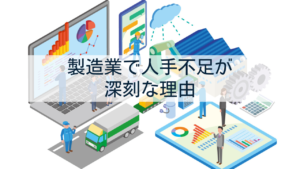
技術継承における課題
多くの企業では職人の「スキル・勘・コツ」を次世代に継承する「技術継承」が大きな課題となっています。
技術継承を進めるためには長年の経験によって培われた「スキル・勘・コツ」といった暗黙知の一部を、デジタル技術を用いて形式知化し、継承可能なかたちにする必要があります。
MESの需要が高まる背景には、製造現場のDX化による技術伝承を推進することのニーズがあると言えます。
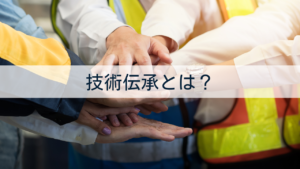
MESを導入する目的
製造業では、MESを導入することで自社利益の最大化を目指しています。そのため、工場での生産活動の効率化が重要となります。
MESを導入することで、売り上げ貢献度の高い工場における生産活動の効率化・最適化が見込まれます。さらに製造現場における情報管理・分析によってリスク要因の抑え込みと品質安定化を実現することで、自社利益の最大化にもつながるでしょう。
MESの業務範囲
MESは、生産管理システムに分類される、製造工程に特化したシステムです。なお、製造業でなされる情報管理は「計画層」「実行層」「制御層」に分類できますが、MESは「実行層」に分類されるシステムです。
MESとERP・制御層との違い
製造業における「計画層」「実行層」「制御層」は、以下のように分類されます。担当者には、それぞれの領域のシステムを連携させて活用することが求められます。
- 計画層:生産における上流の工程。製品の受発注管理やそれに伴う生産計画や販売管理などを担当する基幹システム(ERPなど)
- 実行層:計画層・制御層と連携しつつ、MESのように製造・生産現場での工程管理や製造・生産数、各プロセスの管理を担うシステム
- 制御層:生産設備や機械工具などの制御を担うDCSやPLCのようなシステム
計画層のシステムであるERPは、「Enterprise Resource Planning」の略で「企業資源計画」と表現されます。
ERPは、人材や原材料、設備など資源に関する情報を一元管理するシステムです。MESのように製造に関する情報だけではなく、人事情報や財務情報といった間接的な情報も管理しており、経営判断をする際にも用いられます。
MESの代表的な11の機能
アメリカのMES推進団体であるMESAは、MESに必要な機能として11の機能を定義しています。具体的な機能とそれぞれの特徴は以下です。
なお、MESには、これらの機能が搭載されていますが、すべての機能を使用しなければならないというわけではありません。他のシステムで運用できているもの、自社に必要ないものなどは、状況に合わせて取捨選択すると良いでしょう。
生産資源の配分と監視
生産を行うために必要不可欠な資源であるヒト、設備、原材料の情報を正確に管理し、適切に配分を行う。特に多品種少量生産に対応するために重要な機能となる。
仕様・文書管理
設計図面や生産工程における作業指示書などの作成・管理を行う。また、生産時の記録を管理する機能も担う。
作業のスケジューリング
生産計画に基づいて、それを実行する際の詳細スケジュールを作成する。具体的には、どの工程でどのようなプロセスで生産を行うか、設備やヒトをどう配分するかを明らかにする。
差立・製造指示
現場で生産活動に従事する作業者に対して、製造指示や仕様変更などの情報共有を行う。必要な情報を遅れなく速やかに共有することでロスを削減する。
作業者管理
生産活動を行う作業者の状況を正確に把握し、過負荷にならないように割り当てを最適化する。
工程(プロセス)管理
生産工程の状況を適切に把握し、作業者のサポートを行う。また、設備の状態を監視することで、異常発生時に速やかに復旧対応を行えるように通知を行う。
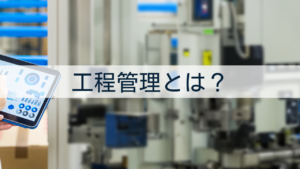
データ収集
各生産工程で計画に対してどの程度作業が進んでいるのかを把握する。また、日時・工程・作業者の情報を紐づけ、現場と間接職場の間で速やかな情報共有を可能にする。
製造の追跡と体系管理
生産途中の仕掛品の追跡、製品履歴を管理する。
実績分析
生産活動の実績を蓄積し分析する。具体的には、生産数や不良に関する情報などの情報に基づいて、原価や品質確保に関する分析を行う。
品質管理
分析したデータを元に、検査業務の管理などに必要な品質管理を行う。
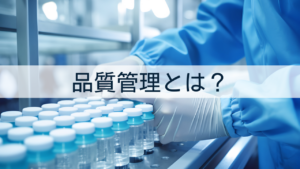
保守・保全管理
設備の定期的なメンテナンスや予防保全を行う際に活用する。適切なタイミングで保守・保全活動を行うことで、突発的な設備停止を防止する。
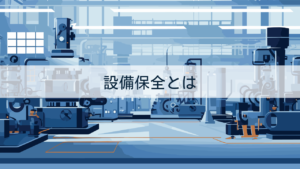
MESの種類
MESには、大きく「オンプレミス型」と「クラウド型」の2種類があります。どちらにも長所・短所があるため、自社の状況や目的に合わせた選定・運用が必要となります。
オンプレミス型
オンプレミス型は、MESに限らず製造業で導入されているさまざまなシステムで採用されている方式です。
システムを構築するために必要なサーバーや各種ソフトウェアをユーザーが所有し、自社のサーバーにシステムを構築します。ユーザーごとにカスタマイズを行うことが可能ですが、システムの運用や保守は自社で管理する必要があります。
MESに自社独自の機能を持たせたい場合などには効果的ですが、初期導入時の機器購入費用や運用・管理コストが必要となるところがデメリットと言えます。また、保守・運用にはスキルが必要であり、自社で人材を育成するか外部に委託する必要があります。
クラウド型
クラウド型では、システムを導入する企業が自社でサーバーやソフトウェアを保有する必要がありません。サービスベンダーが所有するサーバーなどに構築されたシステムをネットワーク上で使用します。
クラウド上で常に最新バージョンに更新されたシステムを使用でき、保守・運用を自社で行う必要がない点、また、初期導入費用が高額にならない点が、主なメリットと言えます。
一方で、提供されるラインナップの中からサービスを選定する必要があり、基本的には自社独自のカスタマイズはできません。また、自社以外のネットワーク上に自社の重要情報を補完・蓄積するため、セキュリティ面でのリスク管理は必要不可欠となります。
MESを導入するメリット
MESを導入するメリットとしては、以下のような項目が挙げられます。
品質の向上
MESを導入することで、生産工程における原材料から最終製品に至る各フェーズを見える化できるため「トレーサビリティ」を確保することができます。これにより、自社製品の品質向上・安定化を実現でき、製品の競争力を高めることにつながります。
また、生産コストの可視化や生産ラインにおけるトラブル未然防止などの効果も期待できます。不良品が流出したり、トラブルが発生したりした場合でも、MESで管理された情報を速やかに共有・分析することで、迅速に対応できます。
多品種少量生産への対応
多品種少量生産では、原材料の在庫管理や各品種の生産量管理、人員などの資源分配を行う難易度が少品種大量生産よりも高くなります。
MESの導入によって、多品種少量生産における在庫・生産量の管理を最適化することで、システマティックに資源状況の監視や分配、作業スケジューリングを行えるようになります。
属人化の解消
MESの仕様・文書管理機能や分析機能を活用すれば、技術系のノウハウをデータ化して共有できます。
各工程で行われる作業の手順をマニュアル化し、そこに経験者が作業時の注意点や勘、コツに関する情報を書き込んでいくことで、業務の標準化を行います。マニュアルを用いて技術継承や新人教育を行えば、属人化の解消を実現できるでしょう。
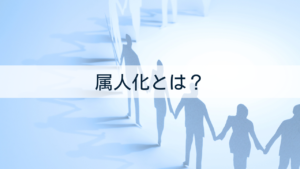
生産性向上(納期短縮・コスト削減)
MESでは、各工程におけるロスを把握して解消していくことができるため、製造現場全体の生産性向上を実現できます。MESによる生産性向上は、納期短縮やコスト削減にもつながります。
部門間の連携強化
MESには、主に生産・製造関連の情報が集約されており、ERPや制御層など他のシステムとの連携も考慮して構築されています。そのため、MESを情報共有の場として活用可能です。
製造担当以外の部門に所属する関係者がMESを確認することで、MESで管理された情報をそれぞれの業務に活用できるようになります。製造現場で突発的なアクシデントが生じても部署間で速やかに必要な情報を共有できるため、スムーズな対応が可能となります。
MES導入時の注意点
MESを導入する際には、以下の点に注意する必要があります。
現場への負担が大きくならないように配慮する
MESを導入する際には、取得・確認すべき情報が増加することで一時的に担当部署の業務負荷が高くなります。そのため運用が定着するまでは注意が必要です。導入計画やメリットをあらかじめ現場で共有しておき、負荷を軽減する体制を構築しておきましょう。
ERPや制御層と連携できるようにする
実行層であるMESはERPや制御層とともに活用するシステムです。これらのシステムと連携することで、MESはその効力を十分に発揮します。 MESを導入する際には、「ERPからMESに受け渡す情報」と「MESから制御層に受け渡す情報」を、「タイミング・粒度・量」などの観点から事前にすり合わせておきましょう。そうすることで導入後のシステム間連携がスムーズに行えま
製造業人材DXの成功事例を公開!
スキル×人材マネジメントなら「Skillnote」が正解!
●製造業で人材DXを成功させるコツがわかる
●スキルマップの作成・運用・データ共有がぺーパーレス化
●スキル管理システムの活用で計画的な人材育成に成功