TPM・TPM活動とは? TPMの8本柱や16大ロス、注目される理由、AI・IoTの有効活用
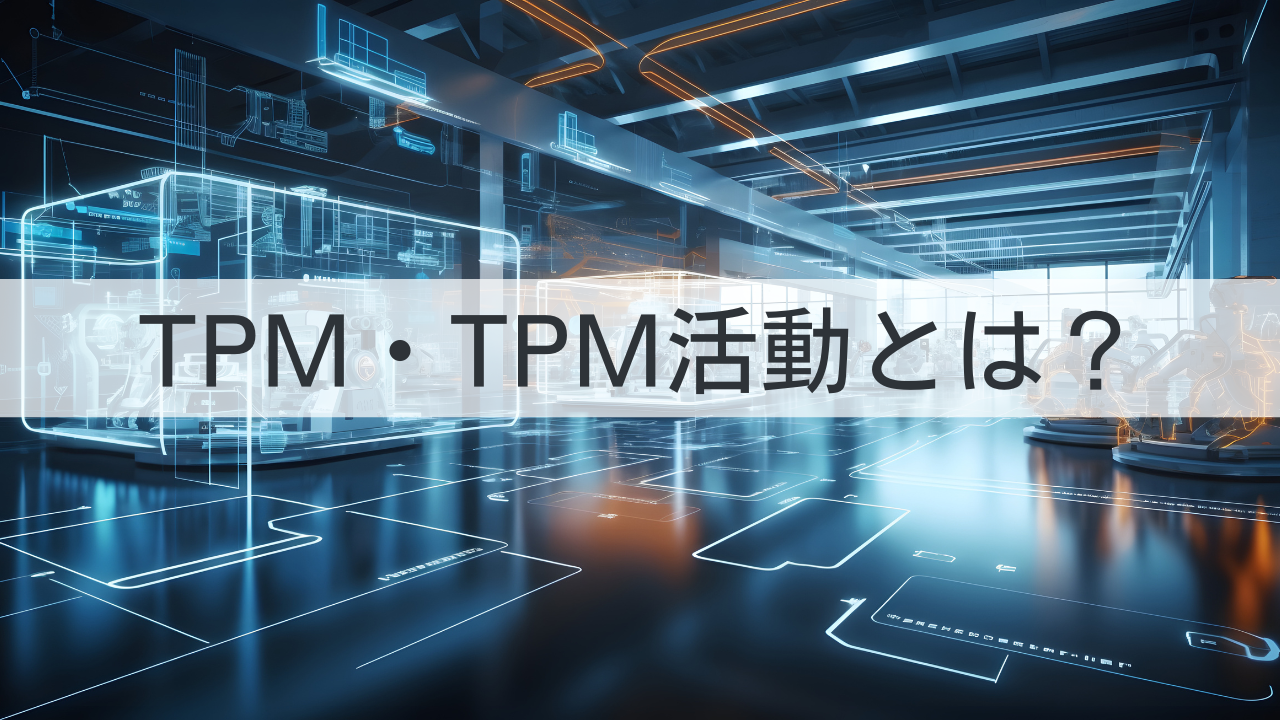
市場環境が厳しくなる中で、企業が競争力を維持・強化するための取り組みとして、TPMに注目が集まっています。TPMは主に製造部門における生産システムに着目した取り組みで、工場だけではなく間接部門も加わることが特徴です。
この記事では、TPMの歴史や概要、導入のメリット、具体的な活動について紹介します。
TPMとは?
TPMとは、「Total Productive Maintenance」もしくは「Total Productive Management」の頭文字を取ったもののこと。工場などの製造部門だけでなく、間接部門も含めた関連するあらゆる部門の人員が全員で取り組む点が特徴と言えます。
なお、自動車産業の品質マネジメントシステム規格である「IATF16949」では、TPMをシステムとして構築することが求められています。
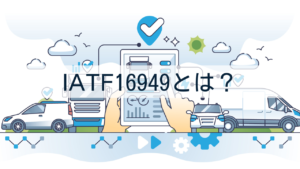
日本プラントメンテナンス協会による定義
製造プラントのメンテナンス技術の発展を目指す公益法人の日本プラントメンテナンスでは、TPMを以下のように定義しています。
“生産システム効率化の極限追求(総合的効率化)をする企業の体質づくりを目標にして、生産システムのライフサイクルを対象とし、“災害ゼロ・不良ゼロ・故障ゼロ”などあらゆるロスを未然防止する仕組みを現場現物で構築し、生産部門をはじめ、開発、営業、管理などの全部門にわたって、トップから第一線従業員に至るまで全員が参加し、重複小集団活動によって、ロス・ゼロを達成すること”
出典:公益社団法人 日本プラントメンテナンス協会「『TPM』とは?」
TPMの目的
日本プラントメンテナンス協会の定義でも表現されているように、TPMでは「生産システムにおけるあらゆるロスをゼロにすること」を目指しています。
ロスをゼロにするために関係者が協力しながら改善アプローチを行うことで、成果を出し続ける仕組みを「現場・現物・現実」で構築していきます。
TPMの5つの基本理念
日本プラントメンテナンス協会は、TPMにおける5つの基本理念を定義しています。
- 儲ける企業体質づくり
- 予防哲学(未然防止)
- 全員参加(参画経営・人間尊重)
- 現場現物主義
- 常識の新陳代謝
TPMでは特に、儲ける企業体質づくりや予防哲学が重要視されており、実際にTPMに取り組む際にはこのことを強く意識する必要があります。
TPMが注目される理由・導入のメリット
TPMがグローバルに注目されるのはなぜなのか。以下ではTPMが注目される理由とTPMを導入することで得られるメリットを紹介します。
市場における競争力強化
市場環境が大きく変化する中で、今後企業が生き残っていくためには市場競争力を強化する必要があります。各企業が必至で対策を講じている中、自社だけが成り行きのままにしていては生き残っていくことはできません。
TPM活動の主要な目的である「さまざまなロスをゼロにすること」が実現できれば、コスト低減や品質の安定化につながります。コスト低減と品質の安定化は、自社の競争力強化に直結するでしょう。
多様化する設備の管理を適正化
生産工場に導入されている設備は、デジタル技術の導入により年々複雑になっています。一方で、長期間使用している高経年化された設備も継続して使われています。現在、生産工場は、形式の異なる設備が混在している状態です。
それぞれの設備に対して保全業務を行う必要がありますが、多様な設備の管理を適正化することは簡単ではありません。しかし、TPM活動によって設備を適正化することができれば、品質と生産効率の両立ができる可能性があります。
従業員全体の意識を深める
TPM活動では、改善活動に関係者全員が参加することが求められています。
工場関連の担当者だけでなく、間接部門も含めさまざまな職種・役職のメンバーが参加することで、お互いの業務に関する理解が深まります。また、役職の差による考え方の違いや意識の違いについても共有でき、従業員全体で生産システムに対する意識を深めることができます。
サステナビリティ経営への対応
TPMは、「サステナビリティ経営」にも効果的です。サステナビリティ経営とは、企業が外部から評価を受ける際の重要な指標のひとつであるため、現在、積極的に取り組む企業が増えています。
TPMでは、安全や環境保全を重視した取り組みを行うため、サステナビリティ経営との相性がよく、取引先や消費者、投資家から高い評価を得られやすくなります。
TPM活動に取り組んでいること自体が、商品選択・投資先選定の判断基準のひとつとなる可能性もあるため、重要な要素と言えるでしょう。
TPMで定義される16大ロス
TPMでは、生産システムにおけるロスを「16大ロス」として定義しています。一般的に、16のロスは大まかに3つに分類されます。以下ではその3分類をそれぞれ解説します。
設備の効率化を阻害する8大ロス
設備の効率化を阻害する「8大ロス」は以下です。主に4Mにおける「Machhine」の領域に含まれています。設備が正常に稼働できない状態や調整などを目的に停止している状態が、8大ロスとして挙げられています。
- 故障ロス
- 段取り・調整ロス
- 刃具交換ロス
- 立上がりロス
- チョコ停・空転ロス
- 速度低下ロス
- 手直し・不良ロス
- シャットダウン(SD)ロス
単に設備の停止時間を減らして稼働時間を長くするだけではなく、設備が稼働中の効率や生産性まで含めて最適化することが大切です。なお、「速度低下ロス」は稼働時間全体に影響するため、改善効果が大きいでしょう。
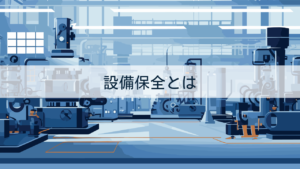
人の効率化を阻害する5大ロス
人の効率化を阻害する「5大ロス」は以下です。主に4Mにおける「Man」の領域に当たります。
- 管理ロス
- 動作ロス
- 編成ロス
- 自動化置き換えロス
- 測定調整ロス
人の効率化を進める際の観点は、単に作業手順の最適化や人員配置の最適化だけではありません。例えば、本来は自動化することで人件費削減や作業効率向上が期待できるのに、実施していない状態などもなくすべきロスとして定義されています。
他にも、設備改修などによって人の手が空いた場合に、空いた時間をどう使うかといったイレギュラーな状態もロスとして考える必要があります。
原単位の効率化を阻害する3大ロス
原単位とは、製品を生産するために必要な原材料や時間、エネルギーを意味します。原単位の効率化を阻害する「3大ロス」は以下です。
- 歩留まりロス
- エネルギーロス
- 型・治工具ロス
3大ロスでは、原材料の歩留まりや原材料を加工・搬送する際に必要となるエネルギーを最適化することを考えます。これらは、4Mにおける「Machine」に分類されることも多いと言えますが、TPMの16大ロスの中では、「原単位」として明確に分けて考えられています。
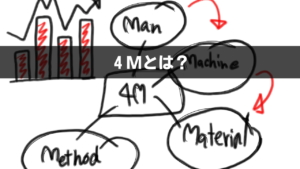
TPMの8本柱(主要な活動)
TPMにおける主要な活動は、以下の8本柱として定義されています。これらの活動の対象は、生産現場だけにとどまらず、経営層や保守・管理部門にも及びます。
生産システムの個別改善
生産システムの個別改善は、設備単体のロスや生産ライン全体における各工程で発生するロスを個別に改善していく活動です。個別に改善・最適化を行うことで、全体としてもロスを削減し全体最適に近づけるという考え方です。
長い間継続され当たり前になっているプロセスに対して、改めて調査をして改善することで従業員の意識改革にもつながります。

オペレーターの自主保全
現場で設備を扱う作業に従事するオペレーターが、担当する設備や業務を自主的に点検し改善する活動もTPMの重要な活動の一部です。
日常的に扱っているオペレーターだからこそ気づける変化があります。小さな変化が生じたタイミングで適宜保全を行うことで、大きな影響を及ぼしかねないロスを防ぎやすくなります。
また、保全担当者以外も設備や設備に関する業務についての知識を身に着けることで、改善提案はしやすくなるでしょう。
保守部門による計画保全
保全業務はオペレーターが行うだけでなく、保守部門が時間をかけてしっかり保全業務を行う必要があります。なお、保守部門が行う設備の故障低減や寿命延長を目的とした計画的な保全業務も、TPMの活動のひとつです。
計画保全では、あらかじめ設備を停止できる計画を立てておくことで、時間をかけて設備のメンテナンスを行います。また、設備自体の保全だけではなく、突発的な故障が生じたときに備えて、速やかに機能回復するための部品の確保や予知・予防保全体制の確立も必要です。
近年は、AI技術を導入した予知保全を行うシステムの構築も進んでいるため、計画保全を適切なタイミングで行えるようになっています。
ロスを最小限にする初期管理
生産時にロスが生じることがあらかじめ想定できる場合には、ロスを最小限にするための初期管理が効果的です。初期管理とは、生産の前段階である製品の設計・開発段階での対策を意味します。
生産現場における過去の情報や生産トライの情報を設計・開発現場にフィードバックすることで、ロスが起きにくい製品・設備・工程の設計につながります。
品質保全体制の確立
製造業におけるロスは生産中だけではなく、製品出荷後に生じることもあります。例えば、不良品の流出や納入先および消費者からのクレームによってロスが生じる、など。これらは改善が必要なロスです。
出荷後のロスを防止するためには、ロスが出にくい製造プロセスを構築したうえで、製品出荷後に不良品が流出しないような検査体制の構築が重要です。工程ごとに品質基準を設け、最後の砦である検査工程で確認すべき項目を正確に測定、判断する手順を決める必要があります。
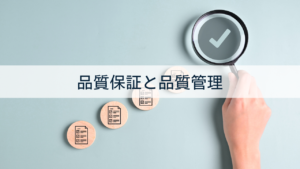
管理・間接部門の保全活動
TPMでは間接部門も含めた全体での取り組みも重要です。生産部門におけるロスを削減するために、管理・間接部門が行える保全活動があります。
例えば、事務所における5S(整理・整頓・清掃・清潔・躾)の徹底や、不要在庫の削減、売り上げ拡大を目指した営業活動等が、管理・間接部門の保全活動に当たります。
教育・訓練プロセスの整備
現場作業者のスキルにばらつきがある状態で標準化を行ってしまうと、標準化後のスキルが低い人員でも対応できるようにフォローする必要(ロス)が生じてしまいます。
そのため、標準化を行う際には必要スキル項目の決定と水準の明確化を事前に行いましょう。また、設定した水準に速やかに到達するための教育・訓練プロセス整備も必要です。
安全・衛生管理の確立
製造現場による事故や災害は、従業員のけがや設備の故障、製品ロスに加えて、従業員の安全管理や設備稼働停止による社会的な影響という観点で大きなインパクトがあります。
事故や災害が発生しないように適切なルールを定め、それをしっかりと守ることを徹底しましょう。また、普段から5Sを心がけることも大切です。
TPMの歴史・変遷
TPMのベースとなったPMは1960年代に始まり、それ以降TPM活動は時代とともに広がっていきました。
当初、TPM活動は生産・保全部門が主体となったものでしたが、時代とともに開発・営業部門も含めた活動、また経営層も含めた活動へと拡大されています。
PM活動から第五世代のTPM活動の変遷は以下となります。
1960年代:TPMの時代
事後保全から予防保全へ転換
1970年代:第一世代のTPM
製造と保全の両輪体制(オペレータによる保全活動)
1980年代:第二世代のTPM
マン・マシンシステムを対象極限追及(設備の極限利用:6大ロス)
TPM5本柱
1990年代:第三世代のTPM
生産システムを対象(生産効率の極限追及:16大ロス) コスト低減、理想コスト追及、TPM8本柱
2000年代:第4世代のTPM
利益追求、キャッシュフロー経営、SCM(デマンドチェーンも含む)
2010年代:第5世代のTPM
アセットマネジメント、環境、IoT、サステナビリティ、保全力、設備・システム診断技術・加工店モニタリング
※参考:日本能率協会コンサルティング(JMAC)の資料
海外におけるTPMの普及
TPMは国内だけでなく海外でも盛んに導入されており、特に1990年代以降にその傾向は加速しています。
その大きな理由の一つとして、TPMに取り組むことで経営指標の改善に加えて部門間のコミュニケーション向上など、間接的なメリットが多くあることが挙げられます。今後もさまざまな企業が導入し、グローバルに広がっていくでしょう。
TPMの実現に必要不可欠なIoT・AIの活用
TPMを高い質で取り組むためには、人の力だけではなくIoTやAIなどのデジタル技術を効果的に活用する必要があります。
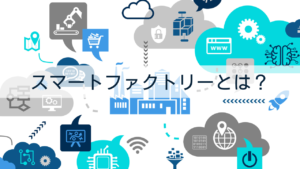
全関係者が共用できるシステムの導入
TPMは部門や役職の垣根を超えて関係者全員が参加する活動のため、関係者全員がアクセスでき、速やかに情報を共有できるシステムを導入する必要があります。
TPM活動のために新たなシステムを導入する場合には、各部門が保有している既存システムとの連携性や使い分けを考慮することが重要です。また、導入したシステムは、実際に運用しながら改善していくことで、TPMの効果を高めることにつながるでしょう。
IoTを用いた現場データの収集
TPMで解消すべきロスの定量的な測定を、人間の力だけで行うのは限界があります。IoT技術を活用することで、人には測定できない精度・量のデータを効率的に取得できます。
取得したデータは、現状把握やTPMにおける活動成果を比較するために必要不可欠なデータとなります。幅広い切り口のデータを収集することが重要です。
IoT・AIを連携させた予知保全の実現
IoTを活用して収集したデータは膨大になるため、人間には処理しきれません。そのため、AIを用いたアルゴリズムを構築・分析する必要があります。
人間の動作解析を行うことで、効率的な作業手順や工程レイアウトを構築できます。また、生産量と発注量の関係などから、在庫として事前に確保しておくべき原材料量の予測などにも活用できるでしょう。
製品の品質向上に導く「技術伝承」を、「スキル管理」で効率化しませんか?
「技術伝承」をシステム化するなら「Skillnote」!
●スキルデータの活用で「技術伝承」の解決策がわかる
●自社に最適化したスキルマップがかんたんに作れる
●「品質向上」に成功した事例を大公開