4M変更とは? 5M+1Eや6Mとの違い、4M変更の手順を解説

製造業では、設備や材料などを変更しなければならない場面が多くあります。しかし、変更内容や、変更の影響があいまいなまま変更を実施すると、思わぬ品質不具合の発生につながります。そのため、4M変更で変更点を整理し、十分に事前評価を行うことが重要です。
この記事では、4M変更の定義、顧客への通知義務(4M変更申請)、5M+1Eや6Mとの違い、4M変更の手順を解説します。顧客に提出する4M変更申請書のExcelフォーマットもダウンロード可能ですので、ぜひ最後までお読みください。
目次
4M変更とは?
4M変更とは、「人(Man)」「設備(Machine)」「材料(Material)」「方法(Method)」という製造プロセスにおける4つの基本要素の変更を指します。製造の過程では、これらの基本要素の変更は避けられません。
- 退職や異動による作業員の変更や、生産量を増やすための作業員の増員
- 老朽化による生産設備の変更、生産設備の増築、生産拠点の変更
- 性能向上のための材料の変更、材料メーカーでの成分変更
- 生産性改善のための作業方法の変更
など、これまでと違う生産プロセスになるケースは数多くあります。 こういった変更の際には、変更の影響で予期せぬ品質不具合が発生しないように管理することが重要です。そのため、4Mの観点から変更点を明確にして、十分に試作や評価を重ねましょう。4M変更は、品質不具合を未然に防ぎ、顧客満足度を高めるうえで欠かせません。
あわせて読みたい

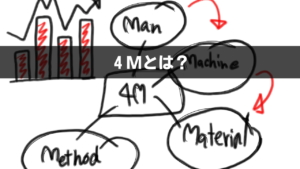
製造業・品質管理の4Mとは? 5M+1Mや6Mとの違い、変更管理、効果の出し方について解説
製造業において「品質」は非常に重要度が高い要素です。品質の低い製品を出荷してしまえば、低品質な製品によって顧客満足度を低下させるだけでなく、安全に関わる問題につながるリスクを負ってしまいます。
しかし、品質はさまざまな要因の影響を受けて決定されるため、その適切な管理は決して簡単なものではありません。そのことから、現在、影響要因を抜けもれなく管理する「4M」を用いて品質を管理する企業が増えています。
この記事では、4Mの概要や4Mを用いた品質管理のメリット、また、4Mを用いた変更点管理について解説します。
4M変更申請とは? 顧客への通知義務
4M変更申請とは、4Mのいずれかを変更する際に、顧客にその内容を通知する手続きです。とくに、自動車業界や医薬品業界など品質基準が厳しい分野では、顧客との契約で事前に承認を得ることが義務付けられているケースもあります。必要に応じて、顧客も変更後のテスト品で試作を行い、品質が保たれていることを確認してからサプライヤーに変更の承認をします。
通知の義務は、製品の種類や変更内容、品質に影響を及ぼす可能性によってさまざまです。顧客への通知を行うかどうかは、顧客との契約を確認したり、顧客に直接質問したりするなどして決定します。
4M変更の基本要素とは?
4M変更の4つの基本要素を詳細に説明します。
人(Man)の変更
4Mにおける「人」とは作業員を指します。製造プロセスにおいて作業員の配置転換や増員などは必ず発生します。作業員のスキルが一定以上となるよう教育体系の構築が重要です。
あわせて読みたい

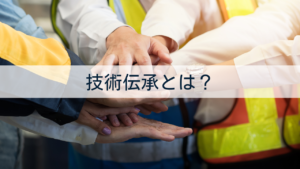
【事例アリ/成功パターン解説】技術伝承とは? 暗黙知と形式知、技能伝承との違い、行わないリスクと成…
製造業など、ものづくりに関わる企業を中心に「技術伝承」という用語が使われています。団塊の世代の定年退職が始まった2007年以降、頻繁に使用されるようになりました。
しかし、技術伝承の当事者となる方の中には、技術伝承という言葉の意味をしっかり把握できていない方も多いのではないでしょうか。
この記事では、技術伝承の概要に加えて、製造業で技術伝承が重要視される理由、実際に技術伝承を進めていく際の課題と対策を紹介します。
あわせて読みたい

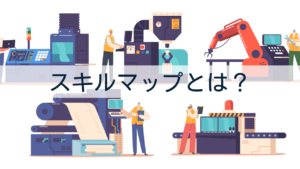
スキルマップとは? 目的、メリット、作り方、トヨタの活用例、職種別の項目例を解説【エクセルテンプレ…
スキルマップは、従業員のスキルを管理するためのツールです。スキルマップの活用によって効率的な人事配置や人材育成が可能になります。
ここでは、スキルマップについて目的や作り方、手順・項目例、目的、活用方法、導入企業、テンプレートなどをご紹介します。
設備(Machine)
4Mにおける「設備」とは、製造プロセスで使用される生産設備のことです。老朽化による設備変更や、生産量を増やすための改造、新規導入が含まれます。また、製造に必要な金型や治具なども設備に当たります。設備の老朽化や不具合は、品質低下や生産停止のリスクがありますので、定期的なメンテナンスが欠かせません。
あわせて読みたい

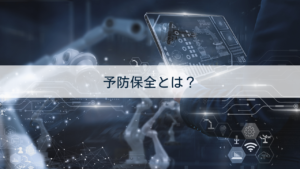
予防保全・予知保全とは? それぞれの違い、事後保全との違い、導入メリット・デメリットを解説
製造業において、品質の安定した製品を継続的に生産・供給するためには、設備保全は必要不可欠です。
しかし、保全業務を行うのは一般的に、設備の不具合や故障が明らかになったタイミングです。設備に不備のある状態のまま生産を継続していると、品質悪化や不良品の増加につながります。また、生産の長期停止などに陥ってしまう恐れがあります。
このような状況を解決するものとして、「予防保全」や「予知保全」が注目を浴びています。この記事では、予防保全・予知保全の定義とメリット・デメリットを紹介します。
材料(Material)
4Mにおける「材料」とは、製品の材料や部品を指します。材料自体を変更するだけではなく、材料を構成する原材料の変更、供給業者の変更、入手ルートの変更、材料の保管方法の変更なども含まれます。材料は製品を構成する一部で、製品品質に大きく関わりますので、慎重な対応が必要です。
方法(Method)
4Mにおける「方法」とは、作業手順や製造プロセス、製造条件を指します。
作業手順を変更する場合には、品質に影響を与えないかの確認が求められます。温度や圧力などの製造条件の変更も同様です。変更が品質に影響を与えないか十分な確認を行います。
また、そもそも作業手順が標準化されていない場合は、作業者ごとに手順が異なり品質がばらつくリスクがあります。作業の標準化は品質の安定化には欠かせません。
あわせて読みたい


業務平準化とは? 意味や標準化との違い、製造業において重要な理由、実現のための具体策
少子高齢化の進行にともない、1995年以降、生産年齢人口の減少が進んでいます。国立社会保障・人口問題研究所によれば、生産年齢人口は2020〜2060年の40年間にかけて約2…
ISO 9001:2015 における4M変更
ISO 9001:2015の規格でも、「8.5.6 変更の管理」で以下の要求事項があります。
組織は、製造又はサービス提供に関する変更を、要求事項への継続的な適合を確実にするために必要な程度まで、レビューし、管理しなければならない。 組織は、変更のレビューの結果、変更を正式に許可した人(又は人々)及びレビューから生じた必要な処置を記載した、文書化した情報を保持しなければならない。
このように4M変更では、変化点を関係者間で共有し、変更の記録を残すことが求められます。あらかじめ4M変更を行う際にレビューのルールを定めておくのが望ましいと言えます。
あわせて読みたい

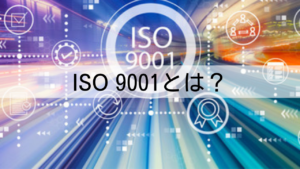
ISO 9001とは? 目的、メリット、要求事項、取得の流れを解説
世界170か国以上、100万以上の組織が認証を取得している品質マネジメントの国際規格「ISO 9001」。
得意先企業に取得を求められたり、外部からの信頼感を醸成したりするために取得を目指す企業も少なくありません。しかし、いざ担当者に任命されたものの何から始めればわからない方も多いのではないでしょうか。
この記事ではISO 9001の概要や取得メリット、取得のために満たす必要のある要求事項、取得までの流れを徹底解説します。
「5M+1E」「6M」と4Mの違い
4Mは製造プロセスに欠かせない基本要素ですが、4Mだけでは足りないという考え方もあります。そのような背景から、4Mの発展形である「5M+1E」や「6M」が生まれました。
5M+1E
5M+1Eは、4Mに「測定(Measurement)」と「環境(Environment)」を加えたものです。
「測定」は製品検査の内容や検査に使う計測機器を指し、品質不具合を顧客に流出させないために重要です。たとえば、精密機器などでは、検査に使う測定機器の測定精度の違いが製品品質に影響を与える場合もあります。
また、「環境」は、製造時や保管時の作業環境(気温・湿度、クリーン度など)を指します。たとえば、半導体部品などでは異物の付着は製品性能に関わるため、クリーン度を徹底的に管理する必要があります。このように製造時の作業環境を変更する場合にも、品質不具合が発生しないよう十分な検証が必要です。
6M
6Mは、4Mに「測定(Measurement)」と「マネジメント(Management)」を加えた考え方です。「測定」は製品検査の内容や検査に使う計測機器を指し、「マネジメント」は、製造プロセス全体の管理や品質マネジメントシステムを意味します。
マネジメントの具体例としては、製造プロセス全体に関わる効率化などの変更、従業員教育体系の変更、あるいは、4M変更時のレビューフローの変更などが挙げられます。
たとえば、軽微な変更だと考えていた材料変更が原因で品質不具合が発生した場合、「なぜ軽微な変更だと考えてしまったのか」「変更時のレビューのやり方に問題がなかったか」といった観点から検証する必要があります。このような観点が6Mの「マネジメント」に当たる部分です。
品質不具合の裏側には、製造プロセス上の個別具体的な変更だけではなく、そもそもの管理方法に原因がある場合もあります。このような意味で、マネジメントの観点も非常に重要です。
品質管理においてなぜ4M変更が重要か?
問題点や改善が必要な点を明確にする
4Mを起点に変更点を管理することで、品質に影響を与える要因を特定できます。
4Mのそれぞれの要素をさらに細かく分析したい場合には、QC7つ道具の1つである特性要因図を用いると便利です。
あわせて読みたい

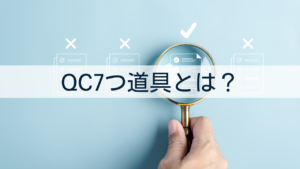
QC7つ道具と新QC7つ道具とは?違いや手法の説明、具体例、覚え方を分かりやすく解説
品質管理において、データによる客観的判断は欠かせません。この客観的判断を助ける7種類の代表的な手法をQC7つ道具と呼びます。QC7つ道具を用いることで、判断精度の向上や属人化からの脱却が見込めます。
本記事では、QC7つ道具と新QC7つ道具の各手法を紹介します。使用する場面やそれぞれの手法を使うことで「分かること」を列挙していますので、「自分の業務でどの手法が使えそうか?」といった視点から、ぜひ参考にしてください。
品質不具合の未然防止
4M変更を適切に管理することで、品質不具合の未然防止が可能です。たとえば、以下のような例が挙げられます。
・材料変更の際に変更後の製品性能が変わる可能性があるため、試作品で問題ないことを十分に確認し4M変更を実施
・しかし、量産が始まると品質不具合が多発し、問題になる
・原因を調査すると、材料変更にともない作業方法も変わっていたため、品質不具合が多発していたことが判明。
以上のケースのように、変更点が複数あった場合にも、事前に4Mに分解し評価していれば、材料だけではなく作業方法にも変更点があったことに気付けます。
このように、4Mの観点で変更点を管理することで、品質不具合の発生リスクを減少させることができます。
柔軟な対応
4M変更の考え方は、少量多品種生産のような柔軟性が求められる製造現場でとくに重要です。少量多品種生産では、切り替え作業が多いため、多くの変更点が生じます。このとき、4Mの観点で変更点を整理し明確にすることで、柔軟な対応が可能になります。
品質改善としての4M変更の手順
以下では、品質改善の取り組みを例に4M変更を行う場合の手順を説明します。
1.課題を設定
まず、4M変更における課題を明確にします。
たとえば、ある製品の不良率削減のため、材料変更による品質改善を行うとすると、4Mのうちの「材料」の部分が変更点となります。
2.4Mの観点から現状分析
次に、4Mを基に変更点が他にないか分析を行います。
先ほどの「材料変更」の例では、「材料」を変更したことに伴い、設備や作業手順、作業員に変更が必要ないかどうか確認します。もし、材料変更に付随して、他にも変更が必要な場合はそちらも変更点として挙げます。
3.事前評価・社内レビュー
変更点が明確になったら、変更前後で不具合がないか事前評価を行います。材料変更の場合であれば、変更後の材料で試作品を作り、性能を評価します。試作の際には、工程能力や不良率、生産性やコストなども十分に検証を行います。
試作後には必要に応じて社内レビューを行い、変更の承認を得ます。
企業によって異なりますが、試作前に検証項目のレビューを実施して、試作後に再度その結果をレビューするケースもあります。
4.変更管理の実施
社内承認が得られたら、実際の製品で4M変更を開始します。試作の段階で課題が出てきた場合はそれを改善してから、実際の4M変更に臨みます。
5.変更管理の評価・改善
変更実施後には変更の効果を分析します。変更後の不良率や生産効率をモニタリングし、目標達成度を評価し、最初に設定した課題を解決できているか検証します。課題解決に至らない場合には、次の案を講じましょう。
顧客への4M変更申請の手順
老朽化による設備の変更や、材料の変更時には、顧客の承認が必要な場合があります。顧客との契約書で4M変更時には申請するよう記載されていたり、製品によっては顧客に変更後の製品の品質評価を依頼したりする場合があります。
1.変更内容とリスクを評価する
顧客への4M変更申請を行う際には、変更の理由や顧客に与える可能性のあるリスクを整理します。変更に伴い製品の性能やコスト、不良率などが変わる可能性があるかどうかを整理して、顧客に説明する準備を行います。
2.顧客からの要求を確認
顧客の求める品質基準や申請のプロセスを事前に把握します。医薬品や自動車業界では、申請内容や申請期限があらかじめ定められているケースもあります。顧客からの要求事項に違反しないよう十分に確認しましょう。
3.事前の社内レビュー
変更を行う前に、変更内容や試作計画を社内レビューで共有し、関係部署の同意を得ます。社内レビューを行うことで申請や試作の精度向上も期待できます。
4.事前に顧客へ4M変更申請を行う
顧客へ変更内容を申請する際は、変更内容の具体的なBfore/Afterと変更の影響を明確に伝えることが求められます。適切な資料やデータを用意して説明すると、顧客の信頼を得やすくなります。
4M変更申請書のテンプレートも準備しておりますので、参考にしてください。
5.試作評価、社内レビュー、顧客への報告
4M変更を行う前には、試作を行い製品性能や工程能力の評価を行うことが一般的です。試作結果を分析し、社内レビューを行い、顧客に報告します。必要に応じて顧客から変更の承認を得てから、4M変更を行います。
作業手順やQC工程表などの文書を変更する場合は、実際に量産品で4M変更を行う前に文書の変更を行っておきます。
あわせて読みたい

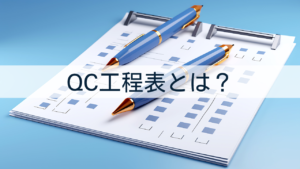
QC工程表とは?作り方、項目例、作業標準書との違い、目的などを解説
製造業では、社是や社訓に品質至上を掲げる企業が多くあります。顧客から求められる品質を確保できない企業はステークホルダーからの信頼を失い、仕事を失ってしまいかねません。品質を重視して業務に取り組むことはとても重要なことです。
製造工程における品質確保や設計と製造の紐づけによる品質確保を行うツールの一つが、QC工程表です。QC工程表を作成することで、関係者で品質に関する情報共有を行い、狙った品質の確保が期待できます。
この記事では、QC工程表の概要やQC工程表が必要とされるシーン、QC工程表に記載すべき項目、作り方などについて紹介します。
6.4M変更を行う
実際の量産品で4M変更を開始します。社内レビューで課題が残っていた場合には、その課題が改善されるよう努めましょう。
7.初期管理を行う
変更後の初期段階では、製品やプロセスのパフォーマンスを詳細に記録し、問題が発生した場合には迅速に対処します。初期管理が安定した品質の確保につながります。
製品の品質向上に導く「技術伝承」を、「スキル管理」で効率化しませんか?
「技術伝承」をシステム化するなら「Skillnote」! ●スキルデータの活用で「技術伝承」の解決策がわかる ●自社に最適化したスキルマップがかんたんに作れる ●「品質向上」に成功した事例を大公開 →詳しくはこちらから
よくある質問
- 4M仕様変更とは何ですか?
-
4M変更とは、「人(Man)」「設備(Machine)」「材料(Material)」「方法(Method)」という製造プロセスにおける4つの基本要素の変更を指します。製造の過程では、これらの基本要素の変更は避けられません。
- 4M変更の義務とは何ですか?
-
4M変更申請とは、4Mのいずれかを変更する際に、顧客にその内容を通知する手続きです。とくに、自動車業界や医薬品業界など品質基準が厳しい分野では、顧客との契約で事前に承認を得ることが義務付けられているケースもあります。必要に応じて、顧客も変更後のテスト品で試作を行い、品質が保たれていることを確認してからサプライヤーに変更の承認をします。
通知の義務は、製品の種類や変更内容、品質に影響を及ぼす可能性によってさまざまです。顧客への通知を行うかどうかは、顧客との契約を確認したり、顧客に直接質問したりするなどして決定します。
- ヒューマンエラーを防止するための4つのMとは?
-
「人(Man)」「設備(Machine)」「材料(Material)」「方法(Method)」という製造プロセスにおける4つの基本要素を指します。