トヨタ式「カイゼン」(活動)とは? 古いとされる理由、目的、3M・5S

製造業の現場で働いている方のなかには、「トヨタ式カイゼン活動」という言葉を聞いたことがある方も多いのではないでしょうか。
また、製造現場で実際に「トヨタ式カイゼン」を活用している方も、少なくないかと思います。「トヨタ式カイゼン」は、海外の製造現場でも活用されており、ワールドワイドな活動としても知られています。
本記事では、「トヨタ式カイゼン」の定義やメリット・デメリット、実際に「トヨタ式カイゼン」を行うにあたってのプロセスを詳しく解説します。
これから、製造現場に「トヨタ式カイゼン」を取り入れようと考えている方には、役立つ情報ですので、ぜひ最後までお読みください。
トヨタ式カイゼンとは?
まず、「トヨタ式カイゼン」の概要について、以下の4点を解説します。
- トヨタ式カイゼンの定義
- 「カイゼン」と「改善」の違い
- トヨタ式カイゼンで解消可能な7つのムダ
- トヨタ生産方式(TPS)とは?
それぞれの項目について、詳しく見ていきましょう。
トヨタ式カイゼンの定義
「トヨタ式カイゼン」とは、世界的な自動車メーカーである「トヨタ自動車」で考案された、生産性および製品品質の向上を図る活動を指します。
実際の製造現場では、製造工程における業務のムダを排除するため、作業や業務のやり方を変える活動を行っています。
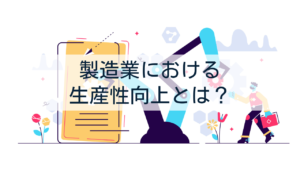
「カイゼン」と「改善」の違い
「カイゼン」と「改善」は一見すると、同じ意味のように思われますが、実は意味が異なる言葉です。
「カイゼン」とは、「現状に満足せず、今よりもっと良くする」という意味を持っています。つまり、カタカナの「カイゼン」では自ら製造現場における課題を認識し、自ら対策を考え、改善していくことがポイントになります。
一方、「改善」とは「悪い部分を良くする」という意味を持っています。つまり、「改善」は悪い点のみ良くする行為であり、「カイゼン」は現状でも問題は無いがさらに業務を良くしていこうという行為になります。
また、「カイゼン」は日本国内だけではなく、世界的にも活用されている考え方です。そのため、「KAIZEN」という英単語になっているほど、浸透しています。
トヨタ式カイゼンで解消可能な7つのムダ
「トヨタ式カイゼン」に取り組むことで、以下の7つのムダが解消できます。
- 加工
- 在庫
- 造りすぎ
- 手待ち
- 動作
- 運搬
- 不良/手直し
加工のムダ
「加工のムダ」とは、必要のない加工や検査を指します。加工のムダがあることで、製造現場の作業者の時間と、製品の原材料にかかるコストが浪費されてしまいます。
在庫のムダ
「在庫のムダ」とは、原材料・部品・仕掛品・完成品などが、余分に保管されていることを指します。これらの在庫のムダがあることで、在庫品の管理コストが余分にかかってしまいます。
造りすぎのムダ
「造りすぎのムダ」とは、必要量以上に余分な仕掛品や完成品を製造してしまうことを指します。「造りすぎのムダ」は、後続の「在庫のムダ」「動作のムダ」「運搬のムダ」の原因ともなるため、7つのムダの中では最悪のムダと呼ばれています。また、余分に造りすぎている間も製造作業は継続されることから、「手待ちのムダ」の遠因にもなっています。
手持ちのムダ
「手待ちのムダ」とは、製造現場の作業者の手元に作業が発生していない、いわゆる「手持無沙汰」な状態を指します。手待ち状態であっても賃金は支払われるため、余分な人件費がかかってしまいます。
動作のムダ
「動作のムダ」とは、製造の進捗に関係しない作業者の動作全てを指します。たとえば、「しゃがむ」「立つ」「探す」などの行為が含まれます。これらの不要の動作は作業者にも負担がかかるため、生産性を向上するためには無くすべきムダです。
運搬のムダ
「運搬のムダ」とは、モノの余計な移動によって発生するムダを指します。前述のとおり、「造りすぎのムダ」によって、生じることが多いです。
不良/手直しのムダ
「不良/手直しのムダ」とは、不良品の発生によって生じる手直しや処分、再出荷で生じるムダのことです。回収、処分、再生産、原因究明、補償に至るまで、不良品の発生は莫大なコストを浪費する懸念があります。
トヨタ生産方式(TPS)とは?
トヨタ生産方式とは、製造工程において発生した7つのムダを解消することで、生産性の向上を実現させるシステムを指します。
トヨタ生産方式を導入することで、ムダなコストが圧縮できるため、企業の収益が向上するといったメリットがあります。
トヨタ式カイゼンの目的・メリット
「トヨタ式カイゼン活動」に取り組むことによって、得られるメリットとしては以下の2点があります。
- ムダを排除し生産性向上・品質向上が図れる
- 従業員の業務に取り組む姿勢の意識改革が達成できる
それぞれのメリットについて、詳しく解説します。
ムダを排除し生産性向上・品質向上が図れる
前述した製造工程における7つのムダを解消することによって、生産性向上・製品品質向上が実現できます。
ムダとなる作業を徹底的に無くしていくことにより、製造現場の作業員の作業効率が高まり、作業員一人ひとりにかかる業務負荷の軽減も図れるといったメリットもあります。
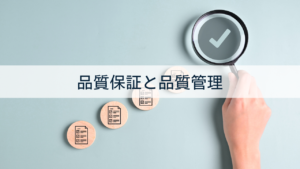
従業員の業務に取り組む姿勢の意識改革が達成できる
「トヨタ式カイゼン」を取り入れることで、従業員一人ひとりが生産性向上・製品品質向上のため、絶えず問題意識を持つようになります。その結果、従業員自らが問題に対する改善策を考えて、行動に移すといった意識を持つようになります。
従業員の意識が変わることによって、組織全体の改善も進むことが期待できます。
トヨタ式カイゼンのデメリット
このように、「トヨタ式カイゼン」に取り組むことによって、さまざまなメリットがある反面、以下の2つのデメリットがあります。
- 企業文化がトヨタと異なる場合にカイゼンの適用に時間がかかる
- 短期的に効果を求める場合には適さない
それぞれのデメリットについて、詳しく見ていきましょう。
企業文化がトヨタと異なる場合にカイゼンの適用に時間がかかる
「トヨタ式カイゼン」に取り組もうとしている企業の文化が、トヨタ自動車と大きく異なる場合には、製造現場でその取り組みが軌道に乗るまで、多大な時間がかかってしまう恐れがあります。
また、既存の製造システムがトヨタ自動車のシステムと大きく異なっている場合にも、「トヨタ式カイゼン」の適用にあたっては、多くの時間が必要となります。
短期的に効果を求める場合には適さない
「トヨタ式カイゼン」は、製造現場におけるムダを調査・分析し、それぞれのムダを解消するために業務のやり方自体を変える必要もあります。
そのため、「トヨタ式カイゼン」に取り組み、業務改善を行うことでムダを解消するためには、多くのマンパワーと一定の時間が必要となります。
よって、短期的に生産性向上・製品品質の向上を図りたい製造現場では、本来「トヨタ式カイゼン」に取り組むことで得られるはずの効果が期待できない場合もあります。
トヨタ式カイゼンは時代遅れなのか?
「トヨタ式カイゼン」は、ムダの排除といった製造業における基本的な業務改善項目が多いため、時代遅れとの声も耳にします。
しかし、製造品質や生産工程の安定が重んじられる製造業においては、「トヨタ式カイゼン」に取り組むことによって得られるメリットの重要性は変わりません。そのため、必ずしも時代遅れとは言い切れないでしょう。
ただし、従来の「トヨタ式カイゼン」をそのまま適用するのではなく、現在のトレンドであるDX・AIなどの活用も必須となることから、日々取り組み内容のアップデートは必要です。

トヨタ式カイゼンの進め方
ここでは、実際に「トヨタ式カイゼン」に取り組む際の進め方について解説します。取り組み方法には、以下の4つのプロセスがあります。
- 製造現場における現状の課題点・問題点の把握
- 課題・問題を解決するためのアイデア出し
- アイデアを実践する
- 実践結果の評価/修正
それぞれのプロセスでやるべき点について、詳しく解説します。
製造現場における現状の課題点・問題点の把握
まず、現在の製造現場における課題点・問題点の洗い出しを行います。これらの洗い出し作業を通じて、「カイゼン」に従事するメンバー間で「カイゼン」を行う目的が明確かつ共有されるため、メンバーの「カイゼン活動」におけるモチベーションのアップが期待できます。
現状の課題点・問題点を洗い出すときには、製造現場における日常作業において、危険に感じる部分や不便に感じる点をピックアップすると、より重要度の高い課題点・問題点が見つけやすいです。
課題・問題を解決するためのアイデア出し
課題点・問題点の洗い出しができれば、次にこれらの点を改善するためのアイデア出しを「カイゼン活動」メンバー内で行います。
アイデアを出す際のポイントとしては、「悪い部分だけにフォーカスを当て過ぎないこと」です。悪い部分だけにフォーカスをあて改善のためのアイデア出しを行ってしまうと、悪い部分が改善した時点で目的が達成してしまい、「カイゼン」がストップしてしまうためです。
そのため、「カイゼン」におけるアイデア出しのときには、「現状を良くするためにはどうしたらいいか」という視点で、アイデアを出すことが重要となります。
アイデアを実践する
アイデアが出尽くしたら、そのアイデアの中から今回の「カイゼン活動」で、実際に取り組むべき対策を決定します。そして対策に沿って「カイゼン」を実行していきます。
「カイゼン」を実行していくなかで、さらに改善すべき点やより良い対策などが出てくる可能性があるため、改善点・対策が新たに出てきた場合には、必ず管理台帳に記載するなど記録を残しておきましょう。
ここで記録した内容が、後続の「実践結果の評価/修正」に大いに役立つためです。
実践結果の評価/修正
最後に、アイデアをベースに決められた「カイゼン活動」を実践した結果について、分析・評価を行いましょう。
具体的には、アイデア出しの際にあらかじめ決めた目標と、実際に「カイゼン」を実施したときの結果のギャップを把握し、そのギャップが発生した原因の分析を行います。
分析後に、今回の「カイゼン活動」の取り組みの評価を行い、実践ではうまくいかなかった点について、さらなる改善策の検討・実施を進めましょう。
トヨタ式カイゼンにおける基本概念
「トヨタ式カイゼン」の基本概念として、「3M」「5S」があります。次に、これらの概念について、詳しく解説します。
3M
3Mとは、製造現場における「ムリ・ムダ・ムラ」を指し、「カイゼン」の基本概念の一つです。
「ムリ」とは、従業員が能力値以上の業務につくことで、負担が大きくなってしまうことを指します。「ムダ」とは、とくに意味を持たない作業のことであり、前述のトヨタの「7つのムダ」も含まれています。「ムラ」とは、製造された製品の品質が一定でない状態のことを指します。
3Mを意識した「カイゼン」に取り組むことで、効果的に業務効率化が図れます。3Mを実施するためには、事前に現状の業務状況を把握しておく必要があります。その理由としては、現状の業務状況を把握していないと、製造作業のどこの部分に3Mがあるのかが分からないためです。
5S
5Sとは、「整理、整頓、清掃、清潔、躾(しつけ)」を指し、3Mと同様に「カイゼン」の基本概念の一つです。5Sは、製造現場の環境を健全にするための活動とも言えます。
整理整頓することで、不要なものが無く、必要なものが適切な場所に保管されるようになります。また、清掃することで埃やごみが少ない現場が実現し、躾が行き届くことで従業員に対する外部からの評価も高まります。
「カイゼン」は対外的な側面でも効果を発揮する活動であるため、5Sは必ずと言っていいほど取り組む価値があるものです。「カイゼン」を取り入れていない企業でも、5Sは製造現場における基本事項として遵守する企業も多いです。
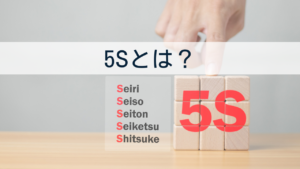
製品の品質向上に導く「技術伝承」を、「スキル管理」で効率化しませんか?
「技術伝承」をシステム化するなら「Skillnote」! ●スキルデータの活用で「技術伝承」の解決策がわかる ●自社に最適化したスキルマップがかんたんに作れる ●「品質向上」に成功した事例を大公開 →詳しくはこちらから
よくある質問
- トヨタのカイゼンとはどういう意味ですか?
-
「トヨタ式カイゼン」とは、世界的な自動車メーカーである「トヨタ自動車」で考案された、生産性および製品品質の向上を図る活動を指します。
実際の製造現場では、製造工程における業務のムダを排除するため、作業や業務のやり方を変える活動を行っています。
- トヨタ式カイゼンはなぜカタカナで書くのですか?
-
「カイゼン」とは、「現状に満足せず、今よりもっと良くする」という意味を持っています。つまり、カタカナの「カイゼン」では自ら製造現場における課題を認識し、自ら対策を考え、改善していくことがポイントになります。
- 改善とカイゼンの違いは何ですか?
-
「改善」とは「悪い部分を良くする」という意味を持っています。つまり、「改善」は悪い点のみ良くする行為であり、「カイゼン」は現状でも問題は無いがさらに業務を良くしていこうという行為になります。