トヨタ生産方式(TPS)とは?基本概念、2本柱、メリットデメリット、導入するための4つの手法や7つのムダについて解説
とは?.png)
日本を代表する企業であるトヨタは、革新的なトヨタ生産方式(TPS)を確立したことでも知られています。
1950年代に開発されたこの生産方式は、製造業の在り方を根本から変革し、現代のものづくりに大きな影響を与え続けています。本記事では、の基本概念からTPSの二本柱、メリット、デメリット、実践手法について解説します。
トヨタ生産方式(TPS)とは?
トヨタ生産方式(Toyota Production System)は、トヨタ自動車が長年の経験とノウハウを積み重ねて確立した独自の生産方式です。
この方式の特徴は、徹底的なムダの排除と品質の作り込みにあります。生産ラインの効率化だけではなく、企業文化や従業員の意識改革までも含む包括的なシステムとして発展してきました。1980年代以降、その効果が世界的に認められ、多くの企業がこの方式を導入しようと試みています。
また、TPSは単なる生産技術ではなく、経営哲学としても評価されており、「カイゼン」や「ジャストインタイム」といった概念は、現代のビジネス用語として広く認知されています。
参考:トヨタ生産方式 | 経営理念 | 企業情報 | トヨタ自動車株式会社 公式企業サイト
フォード生産方式(従来型生産方式)との違い
フォード生産方式は、20世紀初頭にヘンリー・フォードが確立した大量生産方式です。コンベアベルトを使用した流れ作業と作業の細分化により、熟練工ではなくても同じ品質の製品を大量に低価格で生産できる画期的なシステムでした。
一方、TPSは必要な量だけを生産し、在庫を最小限に抑えることで効率を追求します。フォード式が「作れるだけ作る」という考えで過剰在庫になりやすいのに対し、TPSは「必要なものを、必要な時に、必要な量だけ」という考えに基づいています。
リーン方式との違い
リーン方式は、MITスローン経営大学院の研究者ジェームズ・P・ウォマック氏がTPSの考え方を製造業以外の分野にも応用できるよう一般化したものです。
TPSが製造現場に特化した具体的な手法を持つのに対し、リーン方式はより抽象的な概念として、サービス業や医療機関など、さまざまな業界で活用できるように発展しました。基本理念は同じですが、リーン方式はTPSをベースに、より汎用的な改善手法として確立され、海外でも認知度が高いと言われています。
トヨタ生産方式(TPS)の2本柱
トヨタ生産方式(TPS)の基本思想は、「自働化」と「ジャストインタイム」の2本柱です。
1つ目は「ニンベンのついた自働化」で、生産中に何か異常があった場合にすぐに止まるシステムを指しています。2つ目の「ジャストインタイム」は、「必要なものを、必要な時に、必要なだけ作り運ぶ」という考え方です。
両方とも、ムダな作業を徹底的に排除しようという考えから成り立っています。
自働化(ニンベンの働)
自働化は、「機械(自動化)に人間の知恵を与える」という考え方に基づき、「動」の字にニンベンをつけた造語です。 具体的には、生産中に不良品が発生した場合に、機械が自動的に停止したり、作業者自身が停止スイッチを押したりして生産ラインを止められる仕組みの導入です。不良品の流出を防ぐとともに、生産ラインが停止することでその場で徹底的な原因究明が行えます。 また、異常が発生しても機械が自動で停止するので、機械に作業員が張りつく必要がなく、省人化も可能になります。このように少ない人員で品質の良いものを生産できるため、「良いものをより安く」が実現できます。
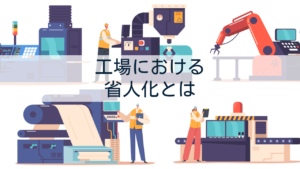
ジャストインタイム
ジャストインタイムは、「必要なものを、必要な時に、必要な量だけ」生産する方式です。ムダな作業を徹底的に排除し、在庫の最小化、リードタイムの短縮、生産効率の向上が実現できます。
具体的には、前工程が持つ完成品のストックを、後工程は必要な部品だけを引き取るようにします。前工程はあらかじめ必要最小限の部品を持っておけるよう、引き取られたらすぐに作って補充します。
クルマの部品は3万点以上に及びますが、この「必要最低限」を全ての工程で行うことで、ムダのない生産活動を実現しています。
「かんばん方式」について
かんばん方式は、ジャストインタイムを実現するための具体的な情報管理ツールです。各工程間で部品や材料の受け渡しを行う際、「かんばん」と呼ばれる情報カードを使用します。このカードには、品名、数量、納入時間などの情報が記載されており、生産の進捗状況をリアルタイムで把握できます。過剰生産や在庫のムダを防ぎ、効率的な生産管理が可能となります。
トヨタ生産方式(TPS)の3つのメリット
トヨタ生産方式(TPS)の導入により、トヨタは世界中で知られる企業になりました。TPSのメリットを改めて解説します。
ムダの排除による原価率の低減や過剰在庫の削減
TPSの導入により、生産工程におけるムダを徹底的に排除でき、大幅なコスト削減が実現できます。とくに、在庫の最適化により、保管コストや在庫管理コストが削減され、資金の効率的な活用が可能となります。
また、不良品の発生が防げれば、材料費や手直し費用も削減できます。さらに、生産リードタイムの短縮により、より迅速な市場対応が可能となり、競争力の向上にもつながります。
このようなムダの排除は、設備の効率的な活用にもつながり、投資効率も向上し、総合的な原価低減を実現します。
人員配置の最適化などによる利益率の向上
TPSの2本柱の1つである「自働化」では、作業員が設備を常時見張る必要から解放されるため、1人の作業員が複数の技能を持つ多能工化が進みやすくなります。 多能工化の推進により、作業者が複数の工程を担当できるようになり、人的資源の効率的な活用が可能です。需要の変動に応じて柔軟な人員配置ができるため、生産性が向上し、人件費の最適化につながります。 また、作業者の技能向上により、品質の向上や工程改善が進み、製品の付加価値も向上します。さらに、チーム単位での改善活動を通じて、組織全体の生産性向上が図られます。
社員の自主性の向上
TPSの2本柱の1つである「自働化」では、異常を生産ラインで見つけ即時に解決することが求められます。
このため、現場作業員の主体的に問題を発見し、解決する能力が重要です。日常的な改善活動をとおして、社員の問題解決能力が向上し、職場の活性化につながります。
また、チーム単位での改善活動により、コミュニケーション能力やリーダーシップも育成されます。社員が自ら考え行動する文化が根付くことで、組織全体の改善力が強化され、持続的な競争力の維持につながります。
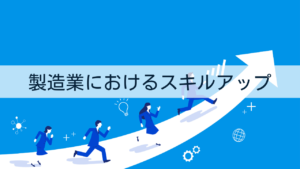
トヨタ生産方式(TPS)のデメリット
前述のようにトヨタ生産方式(TPS)には多くのメリットがありますが、徹底的なムダの排除にはバッファーがないというデメリットも存在します。
納品の遅延や製造ライン停止のリスクがある
在庫を最小限に抑えるジャストインタイム方式では、部品の納入遅延や予期せぬトラブルが発生した場合、製造ラインが停止するリスクが高まります。大規模な設備トラブルや自然災害の影響で、トヨタの生産ラインが停止したというニュースを見たことがある人も多いのではないでしょうか。
このようにジャストインタイム方式では、自然災害や交通障害などの外部要因による影響を受けやすく、サプライチェーンの脆弱性が問題となることがあります。また、需要の急激な変動にも弱く、生産計画の変更への対応が困難な場合があります。これらのリスクに対応するため、適切なバッファーの設定やリスク管理体制の構築が重要となります。
下請け企業に負担がかかりやすい
TPSの厳格な品質管理や納期要求は、下請け企業に負担がかかりやすいと言われています。下請け企業には、高い品質基準の維持や厳密な納期管理が求められ、設備投資や人材育成などの負担が増加します。また、ジャストインタイム生産に対応するため、フレキシブルな生産体制の構築が必要となり、これも大きなコスト要因となります。
小規模な下請け企業にとっては、これらの要求に応えることが経営上の大きな課題となることがあります。
トヨタ生産方式(TPS)は時代遅れなのか?
向く企業・向かない企業がある
TPSは、繰り返し生産が可能な製造業において大きな効果を発揮します。繰り返し生産では、大量生産なのでモノや人、時間のムダが生まれやすくも、逆に同じものを生産するのでムダを削減しやすくもあります。このため、TPSのジャストインタイム生産は大きな効果が生まれます。
一方、一品一様の製品を製造する企業や、プロジェクト型の製造では、標準化された工程管理が難しく、TPSの導入が適していません。また、市場の変動が激しい業界や、製品のライフサイクルが短い業界では、柔軟な生産体制の構築が求められ、TPSの厳格な運用が困難な場合があります。
向く企業・向かない企業がありますので、単にTPSをマネするのではなく、自社での課題解決につながる側面を導入するのがいいでしょう。
トヨタ生産方式(TPS)は時代遅れではない
TPSの基本理念である「ムダの排除」と「継続的改善」は、現代のビジネス環境においても重要な価値を持ち続けています。
とくに、AIやIoT技術との組み合わせにより、より高度な生産管理や品質管理が可能となっています。デジタル技術を活用することで、リアルタイムでの生産状況の把握や、予測的なメンテナンスが可能となり、TPSの効果をさらに高めることができます。また、環境負荷の低減や資源の有効活用という観点からも、TPSの考え方は現代の製造業に不可欠なものとなっています。

トヨタ生産方式(TPS)を導入するための4つの手法
TPSを導入するには、TPSのさまざまな側面を理解しておく必要があります。ここではTPSに欠かせない4つの手法をご紹介します。
手法① 7つのムダどり(製造現場)
TPSでは製造現場には7つのムダがあると言われ、そのムダが生産性の低下やコスト上昇を引き起こしているとされています。製造現場におけるこの7つのムダを特定し徹底的に排除することで、生産効率の向上と原価低減を実現します。
1 つくりすぎのムダ
必要以上の生産は、在庫コストの増加や保管スペースの圧迫につながります。市場需要を正確に把握し、適切な生産量を維持することが重要です。
2 手持ちのムダ
作業の途中で発生する待ち時間や停滞は、生産効率を低下させる要因となります。工程間のバランスを取り、スムーズな生産フローを確立することが必要です。
3 運搬のムダ
不必要な材料や製品の移動は、時間とエネルギーのムダづかいです。レイアウトの最適化や運搬経路の見直しにより、効率化を図ります。
4 加工のムダ
過剰な加工や不必要な工程は、製品の価値を高めることなくコストを増加させます。工程の見直しと標準化により、効率的な生産を実現します。
5 在庫のムダ
過剰な在庫は、保管コストや品質劣化のリスクを増加させます。適切な在庫管理により、必要最小限の在庫水準を維持します。
6 動作のムダ
作業者の不要な動きやムダな動作は、疲労の増加と生産性の低下を招きます。作業環境の改善と動作の標準化により、効率的な作業を実現します。
7 不良をつくるムダ
不良品の発生は、材料や時間のムダになるだけでなく、顧客満足度の低下にもつながります。品質管理の強化と予防措置の徹底により、不良品の発生を防止します。
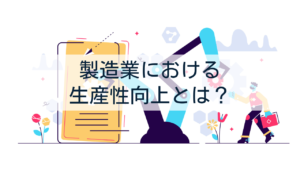
手法① 製造現場以外での7つのムダどり
製造現場だけでなく、事務作業や管理業務においてもムダの排除は重要です。たとえば、不必要に時間の長い会議や過剰な人数の参加する会議は会議のムダと言えます。
価値増しのムダは付加価値を生まない作業の重複を、資料のムダは過剰な資料作成や不要なデータの保管を意味します。調整のムダは部門間の不必要な調整作業を、上司のプライドのムダは過度な承認プロセスや権限の集中を表します。マンネリのムダは慣習的な業務の継続を、ごっこのムダは形式的な活動や実効性のない取り組みを指します。
このように事務作業でもムダは存在しています。これらのムダを排除することで、組織全体の生産性向上が実現できます。
手法② なぜなぜ分析
なぜなぜ分析は、問題の本質的な原因を突き止めるための効果的な手法です。問題が発生した際に「なぜ?」という質問を5回繰り返すことで、表面的な現象から根本的な原因まで掘り下げていきます。
たとえば、製品の不良が発生した場合、「なぜ不良が発生したのか」「なぜその状況が起きたのか」「なぜルールが守られなかったのか?」「なぜルールが不明確だったのか?」と質問を重ねることで、真の原因を特定し、適切な対策を講じることができます。
この手法により、一時的な対症療法ではなく、恒久的な解決策を見出すことが可能となります。
手法③ 問題の見える化
問題の見える化は、現場で発生している問題や課題を、視覚的に分かりやすく表示する手法です。
たとえば、生産状況を示すボード、品質管理図表、工程管理表などを活用し、誰もが現状を即座に把握できるようにします。これにより、問題の早期発見や対策の迅速な実行が可能となります。また、チーム全体での情報共有が促進され、組織的な問題解決能力が向上します。デジタルツールの活用により、リアルタイムでの状況把握や分析も可能となっています。
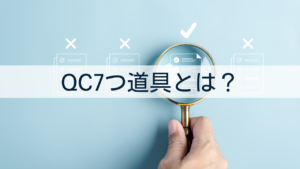
手法④ カイゼン
カイゼンは、より良い製品をより早く、より安価に提供するための継続的な改善活動です。現場の作業者が主体となって、日常的な業務の中から改善点を見出し、実行していきます。小さな改善の積み重ねが、大きな成果につながるという考えに基づいています。
具体的には、作業方法の改善、設備の改良、品質向上、安全性の確保など、様々な側面での改善活動を展開します。カイゼン活動を通じて、従業員の問題解決能力が向上し、職場の活性化にもつながります。また、改善提案制度などを活用することで、全従業員参加型の改善活動を推進することができます。
製造業人材DXの成功事例を公開!
スキル×人材マネジメントなら「Skillnote」が正解! ●製造業で人材DXを成功させるコツがわかる ●スキルマップの作成・運用・データ共有がぺーパーレス化 ●スキル管理システムの活用で計画的な人材育成に成功 →詳しくはこちらから
- トヨタの生産方式とは?
-
トヨタ生産方式(Toyota Production System)は、トヨタ自動車が長年の経験とノウハウを積み重ねて確立した独自の生産方式です。
この方式の特徴は、徹底的なムダの排除と品質の作り込みにあります。生産ラインの効率化だけではなく、企業文化や従業員の意識改革までも含む包括的なシステムとして発展してきました。1980年代以降、その効果が世界的に認められ、多くの企業がこの方式を導入しようと試みています。
- トヨタ生産方式の2つの柱は何ですか?
-
トヨタ生産方式(TPS)の基本思想は、「自働化」と「ジャストインタイム」の2本柱です。
1つ目は「ニンベンのついた自働化」で、生産中に何か異常があった場合にすぐに止まるシステムを指しています。2つ目の「ジャストインタイム」は、「必要なものを、必要な時に、必要なだけ作り運ぶ」という考え方です。
両方とも、ムダな作業を徹底的に排除しようという考えから成り立っています。 - トヨタ生産方式のデメリットは?
-
前述のようにトヨタ生産方式(TPS)には多くのメリットがありますが、徹底的なムダの排除にはバッファーがないというデメリットも存在します。